Vibration-damping device
A vibration attenuation and engine technology, applied in transmissions, fluid transmissions, vibration suppression adjustment, etc., can solve problems such as the negative impact of vibration attenuation performance of rotating bodies
- Summary
- Abstract
- Description
- Claims
- Application Information
AI Technical Summary
Problems solved by technology
Method used
Image
Examples
Embodiment Construction
[0021] Next, modes for implementing the invention of the present disclosure will be described with reference to the drawings.
[0022] figure 1 It is a schematic configuration diagram of the starting device 1 provided with the vibration damping device 20 of the present disclosure. As shown in the figure, the starting device 1 is mounted on a vehicle, for example. The vehicle is provided with an engine (internal combustion engine) EG as a driving device. A front cover 3, a torque converter (fluid transmission) TC, a damper hub 7 as an output member fixed to an input shaft IS of a transmission (power transmission) TM, a lock-up clutch 8, a damper 10, and the like. Here, the torque converter TC includes: a pump wheel (input side fluid transmission element) 4 fixed to the front cover 3 and rotating integrally with the front cover 3; The shaft rotates and is fixed to the driven part 15 of the damper device 10; the stator 6, which rectifies the flow of working oil (working fluid) ...
PUM
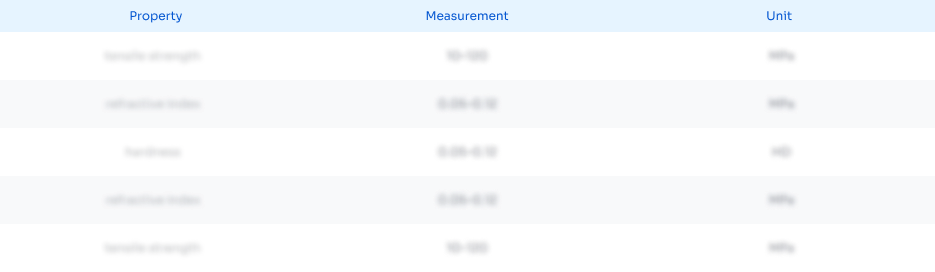
Abstract
Description
Claims
Application Information

- R&D
- Intellectual Property
- Life Sciences
- Materials
- Tech Scout
- Unparalleled Data Quality
- Higher Quality Content
- 60% Fewer Hallucinations
Browse by: Latest US Patents, China's latest patents, Technical Efficacy Thesaurus, Application Domain, Technology Topic, Popular Technical Reports.
© 2025 PatSnap. All rights reserved.Legal|Privacy policy|Modern Slavery Act Transparency Statement|Sitemap|About US| Contact US: help@patsnap.com