Calibration and Verification Method of Shock Temperature Diagnosis System
A diagnostic system and impact temperature technology, applied in radiation pyrometry, optical radiation measurement, instruments, etc., can solve problems such as doubtful reliability of SOP system
- Summary
- Abstract
- Description
- Claims
- Application Information
AI Technical Summary
Problems solved by technology
Method used
Image
Examples
Embodiment 1
[0028] Such as figure 1 and figure 2 As shown, the calibration and verification method of the shock temperature diagnostic system in this embodiment includes the following steps:
[0029] Step 1, establishment of calibration optical path: the calibration optical path includes standard light source 1, first lens 2, target chamber window 3, second lens 4, third lens 5, reflector 6, periscope system 7, fourth lens 8 , a narrow-band channel filter 9 and a streak camera 10, the first lens 2, the target chamber window 3, and the second lens 4 form the first imaging system, the third lens 5, mirror 6, periscope system 7 and The fourth lens 8 forms the second imaging system, and the first imaging system, the second imaging system, the narrow-band channel filter 9 and the streak camera 10 are sequentially placed to form the SOP temperature measurement and diagnosis system, and the light outlet of the standard light source 1 is placed The object plane position before the optical syst...
Embodiment 2
[0038] Such as figure 1 and figure 2 As shown, the calibration and verification method of the shock temperature diagnostic system in this embodiment includes the following steps:
[0039] Step 1, establishment of calibration optical path: the calibration optical path includes standard light source 1, first lens 2, target chamber window 3, second lens 4, third lens 5, reflector 6, periscope system 7, fourth lens 8 , a narrow-band channel filter 9 and a streak camera 10, the first lens 2, the target chamber window 3, and the second lens 4 form the first imaging system, the third lens 5, mirror 6, periscope system 7 and The fourth lens 8 forms the second imaging system, and the first imaging system, the second imaging system, the narrow-band channel filter 9 and the streak camera 10 are sequentially placed to form the SOP temperature measurement and diagnosis system, and the light outlet of the standard light source 1 is placed The position of the object plane in front of the ...
PUM
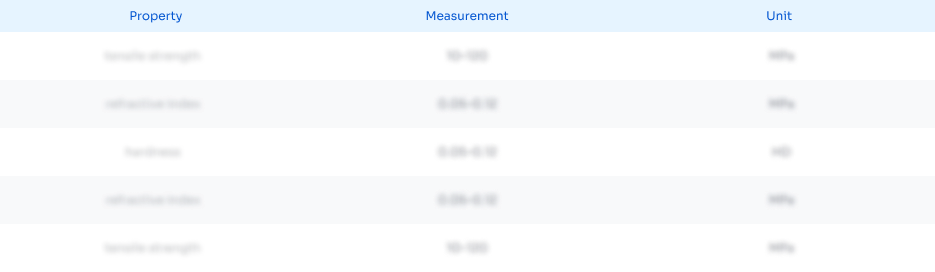
Abstract
Description
Claims
Application Information

- Generate Ideas
- Intellectual Property
- Life Sciences
- Materials
- Tech Scout
- Unparalleled Data Quality
- Higher Quality Content
- 60% Fewer Hallucinations
Browse by: Latest US Patents, China's latest patents, Technical Efficacy Thesaurus, Application Domain, Technology Topic, Popular Technical Reports.
© 2025 PatSnap. All rights reserved.Legal|Privacy policy|Modern Slavery Act Transparency Statement|Sitemap|About US| Contact US: help@patsnap.com