A mems driver based on protruding comb teeth and its working method
A driver and comb-tooth technology, applied in the field of micro-electromechanical, can solve problems such as long-term use of unfavorable lasers and limit the application of lasers, and achieve the effect of facilitating manufacturing and reducing driving voltage
- Summary
- Abstract
- Description
- Claims
- Application Information
AI Technical Summary
Problems solved by technology
Method used
Image
Examples
Embodiment 1
[0043] A MEMS actuator based on protruding comb teeth, such as Figure 1~5 As shown, it includes a movable part 1, a fixed comb 2, a fixed anchor point 3 and a base layer 4, and the fixed comb 2 and the fixed anchor point 3 are fixed on the base layer 4;
[0044] The movable part 1 includes a radial truss 5 , an arc truss 6 , a movable comb 7 and an elastic beam 8 , the arc truss 6 is arranged on the arc position with the imaginary axis point 9 as a circle, and the radial truss 5 is arranged along the radial direction, and the movable comb 7 includes a plurality of movable comb teeth 10, and the movable comb teeth 10 are connected by the radial truss 5 to form the movable comb 7, and the radial truss 5 and the arc truss 6 Connect at the intersection point, the fixed end of the elastic beam 8 is connected with the fixed anchor point 3, the connection method is as follows image 3 As shown, the free end of the elastic beam 8 is connected to the radial truss 5, and the elastic b...
Embodiment 2
[0048] A MEMS driver based on protruding comb teeth, the structure is as shown in embodiment 1, the difference is that all front narrow comb teeth 13 have the same degree corresponding to the central angle of 2 °, and the width of all front narrow comb teeth 13 is It is equal to the central angle multiplied by the corresponding radius, and its width is 5um;
[0049] The center angles corresponding to all the rear-end wide comb teeth 14 are the same, which is 2.5°. The width of the rear-end wide comb teeth 14=central angle*corresponding radius, and the width is 13um.
Embodiment 3
[0051] A MEMS driver based on protruding comb teeth, the structure is as shown in embodiment 1, the difference is that the distance between the two adjacent rear end wide comb teeth 14 of the movable comb teeth 10, and the adjacent two rear end wide comb teeth 14 of the fixed comb teeth 11 The distance between the wide comb teeth 14 at the rear end is 9um.
[0052] When no voltage is applied, the distance H1 between the front narrow comb teeth 13 of the movable comb teeth 10 and the front narrow comb teeth 13 of the fixed comb teeth 11 is 6um to 8um, such as Figure 4 shown. After the voltage is applied, that is, after the front narrow comb teeth are inserted into the rear wide comb teeth, the spacing H2 is preferably 2um, such as Figure 5 As shown, the process requirements are relatively low.
PUM
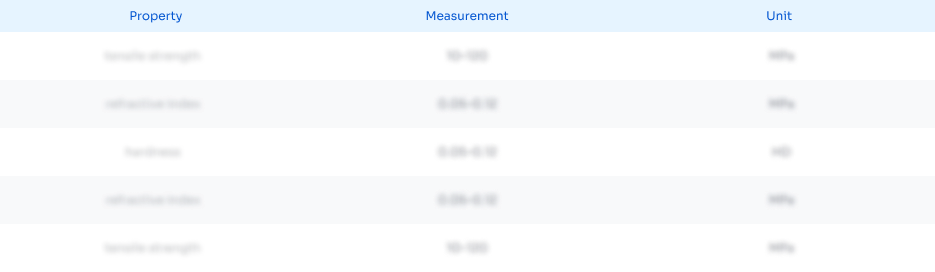
Abstract
Description
Claims
Application Information

- R&D Engineer
- R&D Manager
- IP Professional
- Industry Leading Data Capabilities
- Powerful AI technology
- Patent DNA Extraction
Browse by: Latest US Patents, China's latest patents, Technical Efficacy Thesaurus, Application Domain, Technology Topic, Popular Technical Reports.
© 2024 PatSnap. All rights reserved.Legal|Privacy policy|Modern Slavery Act Transparency Statement|Sitemap|About US| Contact US: help@patsnap.com