Injection mold
A technology for injection molds and mold cores, applied in the field of injection molds, can solve problems such as insufficient exhaust, low efficiency, trapped air, etc., and achieve the effects of eliminating trapped air, improving product quality, and increasing speed
- Summary
- Abstract
- Description
- Claims
- Application Information
AI Technical Summary
Problems solved by technology
Method used
Image
Examples
Embodiment
[0017] In this example, if Figure 1-3 As shown, the injection mold includes: a first mold core 1, a second mold core 2, a third mold core 3, an insert 4 and an exhaust device (not shown), the first mold core 1, the second mold core 2 and The third mold core 3 is arranged in sequence, the second mold core 2 is provided with an inlay channel 21, the third mold core 3 is provided with an exhaust channel 31, and the exhaust channel 31 and the inlay channel 21 are correspondingly arranged, and the exhaust channel 31 is connected to the exhaust channel 21. The air device is connected, the insert 4 is embedded in the inlay channel 21, and there is a gap for air to pass between the insert 4 and the inner wall of the inlay channel 21, when the first mold core 1, the second mold core 2 and the third mold core 3. During injection mold clamping, a cavity is formed between the first mold core 1 and the second mold core 2, the inlay channel 21 communicates with the cavity and the exhaust c...
PUM
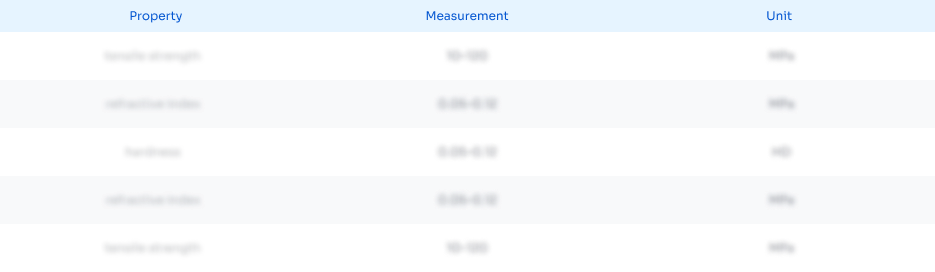
Abstract
Description
Claims
Application Information

- Generate Ideas
- Intellectual Property
- Life Sciences
- Materials
- Tech Scout
- Unparalleled Data Quality
- Higher Quality Content
- 60% Fewer Hallucinations
Browse by: Latest US Patents, China's latest patents, Technical Efficacy Thesaurus, Application Domain, Technology Topic, Popular Technical Reports.
© 2025 PatSnap. All rights reserved.Legal|Privacy policy|Modern Slavery Act Transparency Statement|Sitemap|About US| Contact US: help@patsnap.com