Full-automatic welding machine for small filter elements
A fully automatic welding and filter element technology, applied in welding equipment, welding equipment, auxiliary welding equipment, etc., can solve the problems of inconvenient operation and complicated device structure, and achieve the effect of simple and convenient maintenance, stable filter element quality and convenient replacement
- Summary
- Abstract
- Description
- Claims
- Application Information
AI Technical Summary
Problems solved by technology
Method used
Image
Examples
Embodiment
[0028] A small filter element automatic welding machine, such as figure 1 As shown, it includes frame 1, filter element clamp 9, end cover clamp 10, filter element clamp rail 7, heating bracket 11, filter element heating plate 4, end cover heating plate 3, servo motor 6 and moving cylinder (not shown in the figure) , the end cap fixture 10 is located in the frame 1, used to place the end cap 2, the filter element fixture guide rail 7 is set in the frame 1, the filter element fixture 9 is slidably connected to the filter element fixture guide rail 7, and is used to place the filter element 5 and the servo motor 6 It is used to drive the filter element fixture 9 to move up and down on the filter element fixture guide rail 7. The filter element fixture 9 and the end cover fixture 10 are arranged at intervals up and down and parallel to each other. Between them, the filter element heating plate 4 and the end cover heating plate 3 are respectively arranged on the upper and lower si...
PUM
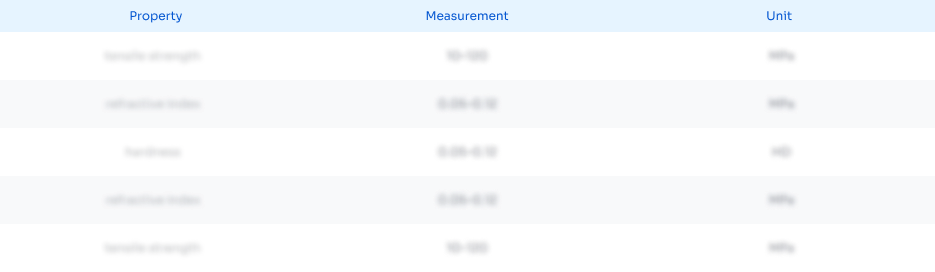
Abstract
Description
Claims
Application Information

- R&D Engineer
- R&D Manager
- IP Professional
- Industry Leading Data Capabilities
- Powerful AI technology
- Patent DNA Extraction
Browse by: Latest US Patents, China's latest patents, Technical Efficacy Thesaurus, Application Domain, Technology Topic, Popular Technical Reports.
© 2024 PatSnap. All rights reserved.Legal|Privacy policy|Modern Slavery Act Transparency Statement|Sitemap|About US| Contact US: help@patsnap.com