Simulation modeling method for jet pipe electro-hydraulic servo valve
A simulation modeling, servo valve technology, applied in the direction of fluid pressure actuation device, fluid pressure actuation system test, mechanical equipment, etc., can solve the problem that the mathematical model of the jet tube servo valve is not given, the performance is not easy to theoretically calculate and predict, Problems such as the research difficulty of jet tube servo valve
- Summary
- Abstract
- Description
- Claims
- Application Information
AI Technical Summary
Problems solved by technology
Method used
Image
Examples
Embodiment Construction
[0054] The present invention will be further described below in conjunction with accompanying drawing.
[0055] The working principle diagram of the jet tube electro-hydraulic servo valve is attached figure 1 As shown: when there is no input current in the coil 1, the armature 2 is supported by the spring tube 13 in the middle position of the upper and lower magnetizers 9, 11, the jet tube 5 and the nozzle 3 are also in the middle position, and the spool valve core is in the middle position of the feedback rod Under the action of 7, it is in the neutral position, and the valve has no hydraulic output; when there is input current in the coil, the armature 2 will deflect, driving the jet tube 5 and nozzle 3 to rotate, and the feedback rod 7 will be deformed at this time. Because the nozzle 3 is offset, the flow rate flowing into the receivers on the left and right sides will be different, and a certain pressure difference will be generated in the left and right chambers of the ...
PUM
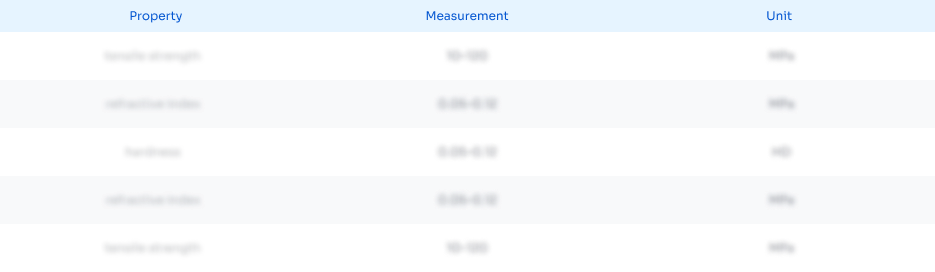
Abstract
Description
Claims
Application Information

- R&D Engineer
- R&D Manager
- IP Professional
- Industry Leading Data Capabilities
- Powerful AI technology
- Patent DNA Extraction
Browse by: Latest US Patents, China's latest patents, Technical Efficacy Thesaurus, Application Domain, Technology Topic, Popular Technical Reports.
© 2024 PatSnap. All rights reserved.Legal|Privacy policy|Modern Slavery Act Transparency Statement|Sitemap|About US| Contact US: help@patsnap.com