Visual positioning method
A technology of visual positioning and positioning holes, applied in the field of visual positioning, can solve the problems of inaccurate positioning of mechanical structures, waste of production beats, time-consuming and other problems, and achieve the effects of improving cycle utilization, high positioning accuracy, and reliable positioning results
- Summary
- Abstract
- Description
- Claims
- Application Information
AI Technical Summary
Problems solved by technology
Method used
Image
Examples
no. 1 example
[0035] Refer to attached image 3 , the method includes:
[0036] Step S10 : After the rolling bed 300 of the automobile production line transports the current vehicle body 400 to the station, control the image acquisition device 120 to capture the positioning image of the positioning structure 410 on the current vehicle body 400 .
[0037]After the rolling bed 300 transports the current vehicle body 400 to the work station, the control device 110 controls the image acquisition device 120 arranged under the rolling bed to photograph the positioning structure 410 at the bottom of the current vehicle body 400 to obtain a positioning image of the positioning structure, and The positioning image is sent to the control device 110 . In the embodiment of the present invention, the positioning structure 410 may be a positioning hole at the bottom of the current vehicle body 400, such as an RPS positioning hole. The RPS system was first invented by the Ford Company of the United Stat...
no. 2 example
[0058] The robot device 500 is applied to the control device 110 in the visual positioning system 100. The visual positioning system 100 also includes an image acquisition device 120 connected to the control device 110. The visual positioning system 100 is installed on the station of the automobile production line, and the station is provided with The robot 200 communicates with the control device 110 . Refer to attached Figure 7 , the visual positioning device 500 includes: an image acquisition module 510 , a pose acquisition module 520 , an offset acquisition module 530 and a robot control module 540 .
[0059] Wherein, the image acquisition module 510 is used to control the image acquisition 120 equipment to collect the positioning image of the positioning structure on the current vehicle body 400 after the rolling bed 300 of the automobile production line transports the current vehicle body 400 to the station; the pose acquisition module 520 is used to Calculate and obta...
PUM
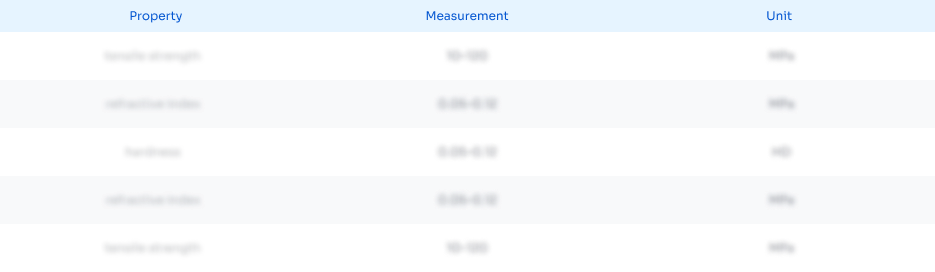
Abstract
Description
Claims
Application Information

- R&D
- Intellectual Property
- Life Sciences
- Materials
- Tech Scout
- Unparalleled Data Quality
- Higher Quality Content
- 60% Fewer Hallucinations
Browse by: Latest US Patents, China's latest patents, Technical Efficacy Thesaurus, Application Domain, Technology Topic, Popular Technical Reports.
© 2025 PatSnap. All rights reserved.Legal|Privacy policy|Modern Slavery Act Transparency Statement|Sitemap|About US| Contact US: help@patsnap.com