Assembly pressing fixture and pressing method for vent screws and screw caps
A technology of exhaust screw and pressing fixture, which is applied in the direction of manufacturing tools, metal processing, metal processing equipment, etc., and can solve the problems of low manual assembly efficiency of exhaust screw and screw cap
- Summary
- Abstract
- Description
- Claims
- Application Information
AI Technical Summary
Problems solved by technology
Method used
Image
Examples
Embodiment Construction
[0024] The technical solutions of the present invention will be clearly and completely described below in conjunction with the accompanying drawings. Obviously, the described embodiments are only preferred embodiments of the present invention, rather than all the embodiments. Based on the embodiments of the present invention, all other embodiments obtained by those of ordinary skill in the art without creative work shall fall within the protection scope of the present invention.
[0025] Such as Figure 1-3 As shown, an assembling and pressing jig for a vent screw and a screw cap includes a mold base 3 on which a lower backing plate 4 is provided, and the lower backing plate 4 is provided with screw plugs in a descending order The cap positioning plate 7 and the exhaust screw positioning plate 6. The screw cap positioning plate 7 is provided with 10 screw cap positioning holes 71, and the shape and size of the screw cap positioning holes 71 are consistent with the shape and size ...
PUM
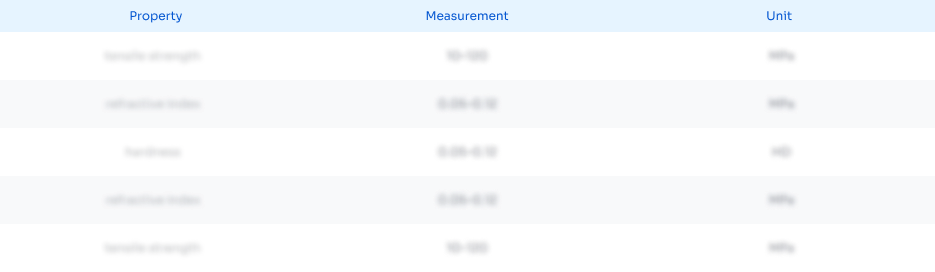
Abstract
Description
Claims
Application Information

- Generate Ideas
- Intellectual Property
- Life Sciences
- Materials
- Tech Scout
- Unparalleled Data Quality
- Higher Quality Content
- 60% Fewer Hallucinations
Browse by: Latest US Patents, China's latest patents, Technical Efficacy Thesaurus, Application Domain, Technology Topic, Popular Technical Reports.
© 2025 PatSnap. All rights reserved.Legal|Privacy policy|Modern Slavery Act Transparency Statement|Sitemap|About US| Contact US: help@patsnap.com