High-speed kerve cold forming machine
A cold forming machine and cold forming technology, which is applied to the driving device of metal rolling mill, metal rolling, manufacturing tools, etc., can solve the problems of unstable product quality and low equipment efficiency, and can overcome bending deformation, Smooth transmission
- Summary
- Abstract
- Description
- Claims
- Application Information
AI Technical Summary
Problems solved by technology
Method used
Image
Examples
Embodiment Construction
[0097] In order to enable those skilled in the art to better understand the solution of the present invention, the present invention will be further described in detail below in conjunction with the accompanying drawings and specific embodiments.
[0098] Please refer to Figure 1-37 , a kind of high-speed workpiece cold forming machine provided by the present invention comprises: power transmission mechanism 1, cold press forming mechanism 2, flattening mechanism 3, cutting mechanism 4 and cooling mechanism; Described power transmission mechanism 1 and described cold press forming mechanism 2; the cold press forming mechanism 2, leveling mechanism 3, cutting mechanism 4 and cooling mechanism are arranged in sequence according to the moving direction of the workpiece; it should be understood that the sequential arrangement means that the above-mentioned mechanisms are in accordance with each process Arranged and arranged, the workpiece is first transported to the cold press fo...
PUM
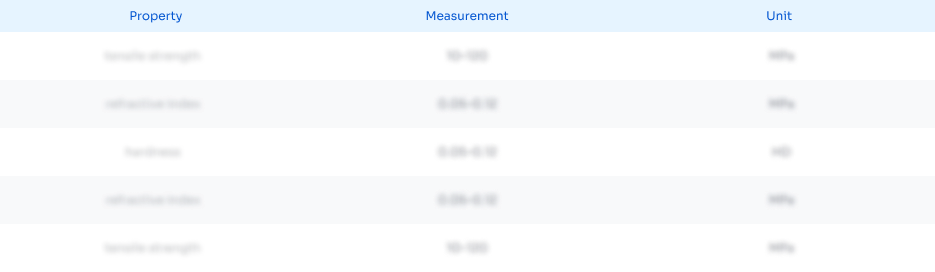
Abstract
Description
Claims
Application Information

- Generate Ideas
- Intellectual Property
- Life Sciences
- Materials
- Tech Scout
- Unparalleled Data Quality
- Higher Quality Content
- 60% Fewer Hallucinations
Browse by: Latest US Patents, China's latest patents, Technical Efficacy Thesaurus, Application Domain, Technology Topic, Popular Technical Reports.
© 2025 PatSnap. All rights reserved.Legal|Privacy policy|Modern Slavery Act Transparency Statement|Sitemap|About US| Contact US: help@patsnap.com