Composite defoaming agent and preparation method thereof
A defoamer and catalyst technology, applied in the field of composite defoamer and its preparation, can solve the problems of single type of defoamer, long defoaming time, short foam suppression time, etc., achieve good surface activity, improve defoaming and inhibiting Foam performance, the effect of ensuring stability
- Summary
- Abstract
- Description
- Claims
- Application Information
AI Technical Summary
Problems solved by technology
Method used
Image
Examples
preparation example Construction
[0022] In order to achieve the above object, the invention provides a kind of preparation method of composite defoamer, wherein, comprise the following steps:
[0023] 1) Stearic acid and antioxidant are mixed and heated to a temperature of 80-100° C. until the stearic acid is melted to obtain a mixed solution X1; after adding ethylenediamine and the first catalyst to the mixed solution X1, the temperature is Stir and mix for 3-5 hours under the condition of 140-150°C to prepare the base material Y1;
[0024] 2) In the presence of the second catalyst and at a temperature of 80-100°C, mix hydrogen-containing silicone oil and allyl polyoxyethylene polyoxypropylene ether to prepare the base material Y2;
[0025] 3) In the presence of the third catalyst, put silicon dioxide and simethicone oil at a temperature of 150-180°C for a mixed reaction for 4-6 hours to prepare the base material Y3;
[0026] 4) mixing and emulsifying base material Y1, base material Y2, base material Y3 and...
Embodiment 1
[0039] 1) 56.9g (0.2mol) of stearic acid and a concentration of 0.3% by weight sodium bisulfite aqueous solution (wherein the content of sodium bisulfite in the solution is 0.123g) are mixed and heated to a temperature of 80°C, until the stearin Acid is melted, and mixed solution X1 is obtained; In mixed solution X1, add 4.808g (0.08mol) ethylenediamine and concentration after being 0.5% by weight phosphoric acid aqueous solution (wherein, the content of phosphoric acid in the solution is 0.247g), at a temperature of 140 Stir and mix for 3 hours under the condition of ℃ to prepare the base material Y1;
[0040] 2) In the presence of an isopropanol solution of 1% by weight of chloroplatinic acid (wherein the content of chloroplatinic acid in the solution is 0.001% by weight), and the temperature is 80°C, 1 part by weight of hydrogen-containing Silicone oil is mixed with 0.8 parts by weight of allyl polyoxyethylene polyoxypropylene ether to prepare base material Y2;
[0041] 3)...
Embodiment 2
[0044] 1) 56.9g (0.2mol) of stearic acid and 0.3% by weight of sodium bisulfite aqueous solution (wherein the content of sodium bisulfite in the solution is 0.330g) are mixed and heated to a temperature of 100°C until stearic acid melts , to prepare mixed solution X1; after adding 9.015g (0.15mol) ethylenediamine and 0.5% by weight phosphoric acid aqueous solution (wherein, the content of phosphoric acid in the solution is 0.461g) to mixed solution X1, under the condition that temperature is 150 ℃ Stir and mix for 5 hours to prepare the base material Y1;
[0045] 2) In the presence of an isopropanol solution of 1% by weight of chloroplatinic acid (wherein the content of chloroplatinic acid in the solution is 0.003% by weight), and the temperature is 100°C, 1 part by weight of hydrogen-containing Silicone oil is mixed with 1.2 parts by weight of allyl polyoxyethylene polyoxypropylene ether to prepare base material Y2;
[0046] 3) In the presence of 0.01 parts by weight of olei...
PUM
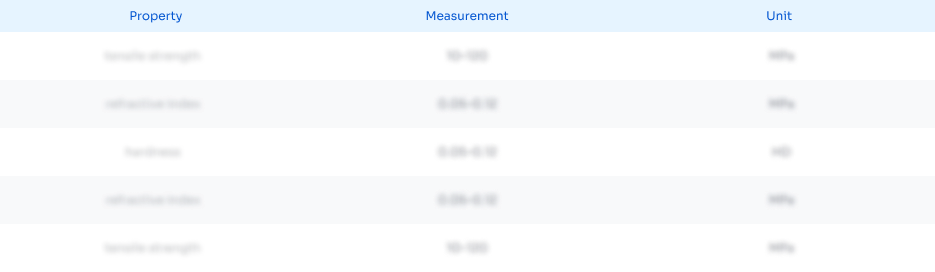
Abstract
Description
Claims
Application Information

- R&D
- Intellectual Property
- Life Sciences
- Materials
- Tech Scout
- Unparalleled Data Quality
- Higher Quality Content
- 60% Fewer Hallucinations
Browse by: Latest US Patents, China's latest patents, Technical Efficacy Thesaurus, Application Domain, Technology Topic, Popular Technical Reports.
© 2025 PatSnap. All rights reserved.Legal|Privacy policy|Modern Slavery Act Transparency Statement|Sitemap|About US| Contact US: help@patsnap.com