Tapered roller bearing assembling device and working method thereof
A tapered roller bearing and sleeve-fitting technology, which is applied to bearing components, shafts and bearings, mechanical equipment, etc., can solve the problem of the large number of lift plates and transfer plates, no quick riveting device, and increased roller friction damage. and other problems, to achieve the effect of saving labor costs, convenient feeding, and rapid riveting
- Summary
- Abstract
- Description
- Claims
- Application Information
AI Technical Summary
Problems solved by technology
Method used
Image
Examples
Embodiment 1
[0039] Referring to the accompanying drawings, the present invention provides a tapered roller bearing assembly device, which includes an operating platform, and is characterized in that it also includes a feeding device, a feeding device, an operating panel, a transmission device, and a riveting device;
[0040] The feeding device is installed on one side of the console and includes a support frame 1, a feeding motor 2 and a hopper 4; the bottom of the support frame 1 is fixed with a feeding motor 2, and the output shaft of the feeding motor is connected to a gear. The gear is connected with the hopper 4 through the chain 3; the hopper 4 is installed on the support frame 1, and the support frame 1 is installed at an inclination here, and a slide rail is installed on the support frame 1, and the bottom end of the hopper is connected with a The chute, under the action of the feeding motor 2, the feeding motor 2 rotates positively and negatively, and the chain 3 drives the hopper...
Embodiment 2
[0054] The working method of the above-mentioned tapered roller bearing assembly device includes the following steps:
[0055] Step 1: Feeding: After the manual switch controls the feeding motor 2 to feed, turn on the corresponding switch of the controller, the feeding cylinder acts, and transfers the tapered rollers to the feeding section. The photoelectric switch 18 monitors the number of rollers in the feeding trough. When the number of rollers is too much, the feedback signal controller, the controller transmits a signal to the feeding cylinder, and the feeding cylinder stops moving and stops feeding; at the same time, the rollers directly fall into the feeding trough;
[0056] Step 2: Cutting the material and forming the initial product: through the two oppositely rolling rollers 19 set at an inclination, the rollers are moved in the direction of the material tube 10, and the fan blades 16 are rotated to screen the direction of the rollers. When the bottom surface of the ...
PUM
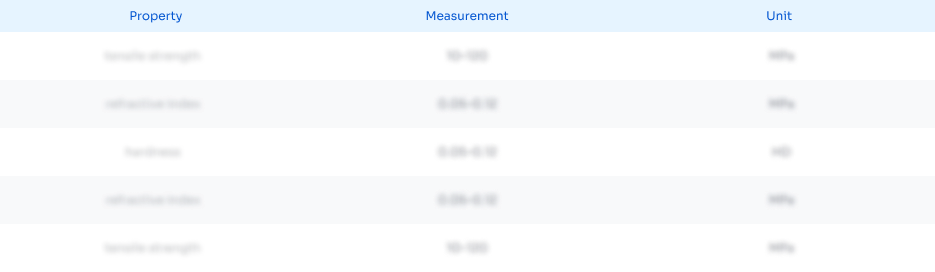
Abstract
Description
Claims
Application Information

- R&D Engineer
- R&D Manager
- IP Professional
- Industry Leading Data Capabilities
- Powerful AI technology
- Patent DNA Extraction
Browse by: Latest US Patents, China's latest patents, Technical Efficacy Thesaurus, Application Domain, Technology Topic, Popular Technical Reports.
© 2024 PatSnap. All rights reserved.Legal|Privacy policy|Modern Slavery Act Transparency Statement|Sitemap|About US| Contact US: help@patsnap.com