Calibrating method and device of tool coordinate system as well as computer-readable storage medium
A tool coordinate system and calibration method technology, applied in the tool coordinate system calibration method, computer-readable storage media, and device fields, can solve the problems of time-consuming, laborious, high cost, etc., achieve reduced requirements, simplify the calibration process and, The effect of reducing the amount of related error brought in
- Summary
- Abstract
- Description
- Claims
- Application Information
AI Technical Summary
Problems solved by technology
Method used
Image
Examples
Embodiment Construction
[0054] In order to make the purpose, technical solutions and advantages of the embodiments of this application clearer, the technical solutions in the embodiments of this application will be described clearly and completely in conjunction with the drawings in the embodiments of this application. Obviously, the described embodiments These are a part of the embodiments of this application, but not all of the embodiments. Based on the embodiments in this application, all other embodiments obtained by those of ordinary skill in the art without creative work shall fall within the protection scope of this application.
[0055] figure 1 A method for calibrating a tool coordinate system provided in an embodiment of this application is applied to an industrial robot. The calibration method includes the following steps:
[0056] S101. Adjust a preset joint of the target robot to a preset position.
[0057] S102: Collect feature points of the end tool connected to the preset joint.
[0058] S10...
PUM
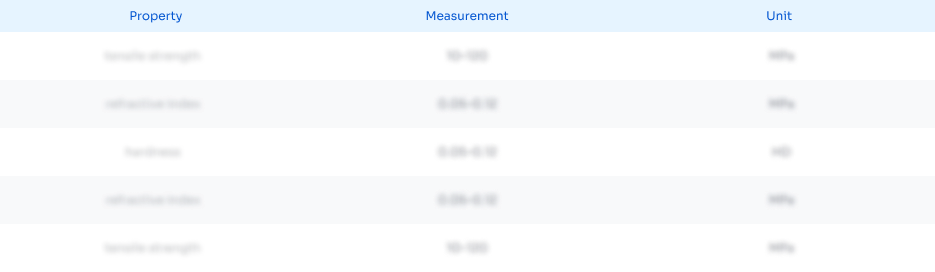
Abstract
Description
Claims
Application Information

- R&D
- Intellectual Property
- Life Sciences
- Materials
- Tech Scout
- Unparalleled Data Quality
- Higher Quality Content
- 60% Fewer Hallucinations
Browse by: Latest US Patents, China's latest patents, Technical Efficacy Thesaurus, Application Domain, Technology Topic, Popular Technical Reports.
© 2025 PatSnap. All rights reserved.Legal|Privacy policy|Modern Slavery Act Transparency Statement|Sitemap|About US| Contact US: help@patsnap.com