Plastic floor forming method with layered structure of woven fabric.
A technology of plastic flooring and layered structure, applied in the direction of chemical instruments and methods, lamination, layered products, etc., can solve problems such as troublesome manufacturing process, time-consuming, environmental damage, etc., and achieve the effect of enhancing the sense of touch
- Summary
- Abstract
- Description
- Claims
- Application Information
AI Technical Summary
Problems solved by technology
Method used
Image
Examples
Embodiment Construction
[0043] see Figure 1-Figure 14As shown, the plastic floor molding method of the woven fabric layered structure of the present invention includes a plastic floor 10. The plastic floor 10 is composed of at least a substrate 11 and a woven layer 13. The substrate 11 can be a rigid single-layer structure or different soft, For the rigid multi-layer structure, a back pad 16 can also be provided on the bottom surface of the substrate 11 as required, and the molding process uses an extruder 20, a first unwinding mechanism 31, a second unwinding mechanism 32, and a third unwinding mechanism. The mechanism 33 and the rolling unit 40 are manufactured and formed in an automated manner, and the forming steps are as follows:
[0044] A. Molding the substrate 11, such as Figure 4 , if the substrate 11 is a rigid single-layer structure, the following formulations can be added using a single extruder 20: polyvinyl chloride resin (PVC) 22-37.5% by weight, calcium carbonate 56-74% by weight, ...
PUM
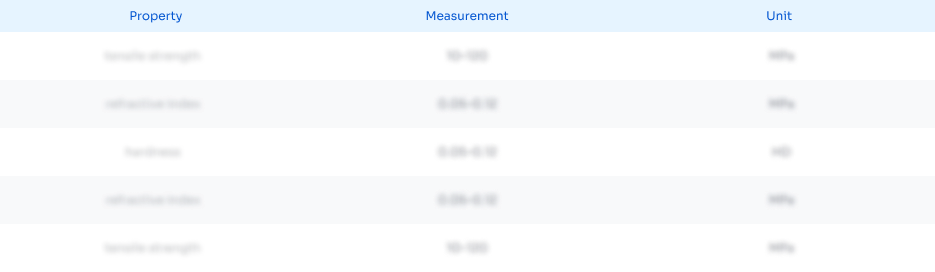
Abstract
Description
Claims
Application Information

- R&D
- Intellectual Property
- Life Sciences
- Materials
- Tech Scout
- Unparalleled Data Quality
- Higher Quality Content
- 60% Fewer Hallucinations
Browse by: Latest US Patents, China's latest patents, Technical Efficacy Thesaurus, Application Domain, Technology Topic, Popular Technical Reports.
© 2025 PatSnap. All rights reserved.Legal|Privacy policy|Modern Slavery Act Transparency Statement|Sitemap|About US| Contact US: help@patsnap.com