Modified plastic color masterbatch and preparation method thereof
A color masterbatch and plastic technology, applied in the field of color masterbatch, can solve the problems that the color material can not be completely uniform, uneven coloring, etc., and achieve the effect of uniform oxidation resistance
- Summary
- Abstract
- Description
- Claims
- Application Information
AI Technical Summary
Problems solved by technology
Method used
Image
Examples
Embodiment 1
[0034] The specific preparation process of colored polyacrylamide resin is as follows:
[0035] Step 1, take 1kg of the mixture of peanut oil and soybean oil, add 350g of sodium hydroxide solution with a mass fraction of 10% to it, raise the temperature to 80°C and stir for 2 hours, pour the product into a separatory funnel and let it stand for 30 minutes to separate layers, the lower layer It is the water phase after saponification, and the upper layer is oil that has not been completely saponified, and the upper layer is obtained by layering;
[0036] Step 2, dissolve 100g of pigments and fillers in 900mL of water, then add 62g of maleic anhydride, 10g of p-toluenesulfonic acid and 85mL of SP-80 into it, stir and mix evenly;
[0037] Step 3: After heating up to 75°C, add 380 mL of the upper layer solution prepared in Step 1 dropwise to the mixed solution in Step 2, stir while adding, and react at a constant temperature for 1 hour after the addition is complete, then filter a...
Embodiment 2
[0040] The specific preparation process of colored polyacrylamide resin is as follows:
[0041] Step 1, take 1kg of the mixture of palm oil and tung oil, add 370g of sodium hydroxide solution with a mass fraction of 10% to it, heat up to 80°C and stir for 2h, pour the product into a separatory funnel and let it stand for 30min to separate layers, the lower layer It is the water phase after saponification, and the upper layer is oil that has not been completely saponified, and the upper layer is obtained by layering;
[0042] Step 2, dissolve 100g of pigments and fillers in 1L of water, then add 68g of maleic anhydride, 11g of p-toluenesulfonic acid and 93mL of SP-80 into it, stir and mix evenly;
[0043] Step 3, after heating up to 75°C, add 440mL of the upper layer solution prepared in step 1 dropwise to the mixed solution in step 2, stir while adding, and react at a constant temperature for 1 hour after the addition is complete, then filter and wash to obtain a surface-adher...
Embodiment 3
[0046] The specific preparation process of colored polyacrylamide resin is as follows:
[0047] Step 1, take 1kg of the mixture of peanut oil and soybean oil, add 350g of sodium hydroxide solution with a mass fraction of 10% to it, raise the temperature to 80°C and stir for 2 hours, pour the product into a separatory funnel and let it stand for 30 minutes to separate layers, the lower layer It is the water phase after saponification, and the upper layer is oil that has not been completely saponified, and the upper layer is obtained by layering;
[0048] Step 2, dissolve 100g of pigments and fillers in 900mL of water, then add 62g of maleic anhydride, 10g of p-toluenesulfonic acid and 85mL of SP-80 into it, stir and mix evenly;
[0049] Step 3: After heating up to 75°C, add 380 mL of the upper layer solution prepared in Step 1 dropwise to the mixed solution in Step 2, stir while adding, and react at a constant temperature for 1 hour after the addition is complete, then filter a...
PUM
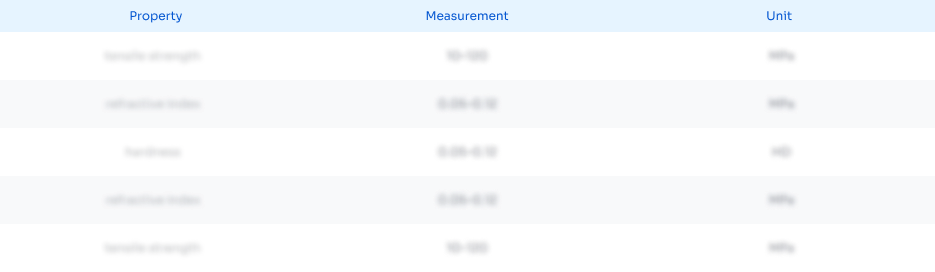
Abstract
Description
Claims
Application Information

- Generate Ideas
- Intellectual Property
- Life Sciences
- Materials
- Tech Scout
- Unparalleled Data Quality
- Higher Quality Content
- 60% Fewer Hallucinations
Browse by: Latest US Patents, China's latest patents, Technical Efficacy Thesaurus, Application Domain, Technology Topic, Popular Technical Reports.
© 2025 PatSnap. All rights reserved.Legal|Privacy policy|Modern Slavery Act Transparency Statement|Sitemap|About US| Contact US: help@patsnap.com