Joint load measurement method based on strain identification multi-joint
A technology of load measurement and multiple joints, which is applied in the direction of measuring devices, force/torque/work measuring instruments, aircraft component testing, etc., can solve the problems that the equation does not meet the Picard condition, is different, and it is difficult to measure the load of multiple joints, and achieves Overcoming the effect of measuring loads
- Summary
- Abstract
- Description
- Claims
- Application Information
AI Technical Summary
Problems solved by technology
Method used
Image
Examples
Embodiment Construction
[0033] In order to make the technical means, creative features, goals and effects achieved by the present invention easy to understand, the present invention will be further described below in conjunction with specific illustrations.
[0034] The joint load measurement method based on strain identification of multiple joints, the specific steps are as follows:
[0035] 1) To calibrate the load, first disassemble the butt joint structural parts, and then select one of the structural parts for calibration, such as figure 1 As shown, select the first connector A 1 Load step by step along the x direction, a total of 8 levels are loaded, record the load F 1 with each strain ε i1 The value of the linear fitting of the load F 1 with each strain ε i1 The relationship between the straight line, get 3m slope k i1 ,then:
[0036]
[0037] For each joint, it is calibrated in the same way in any direction to form the transfer coefficient matrix between strain and load
[0038] ...
PUM
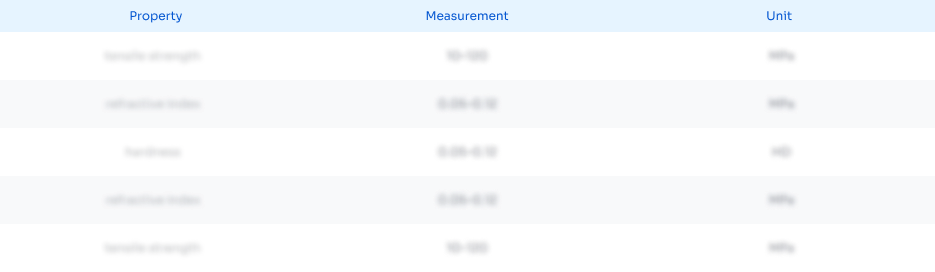
Abstract
Description
Claims
Application Information

- R&D
- Intellectual Property
- Life Sciences
- Materials
- Tech Scout
- Unparalleled Data Quality
- Higher Quality Content
- 60% Fewer Hallucinations
Browse by: Latest US Patents, China's latest patents, Technical Efficacy Thesaurus, Application Domain, Technology Topic, Popular Technical Reports.
© 2025 PatSnap. All rights reserved.Legal|Privacy policy|Modern Slavery Act Transparency Statement|Sitemap|About US| Contact US: help@patsnap.com