Aircraft with load reducing wing like element
A technology for aircraft and components, applied in the field of aircraft, can solve the problems of small contour depth and thickness obstruction, and achieve the effect of reducing the total load
- Summary
- Abstract
- Description
- Claims
- Application Information
AI Technical Summary
Problems solved by technology
Method used
Image
Examples
Embodiment Construction
[0045] Figure 1a Shown is a wing 2 attached to the fuselage (not shown) of the aircraft, the wing 2 having a wing end 4 to which a wingtip arrangement 6 is mounted. Exemplarily, the wingtip device 6 comprises a planar winglet 8 and a curved transition region 10 extending between a connection region 12 of the planar winglet 8 and the wing end 4 of the wing 2 . The planar winglets 8 extend approximately at right angles to the xy plane of the aircraft. Due to aerodynamic and mass forces, the wingtip arrangement 6 generates additional structural loads on the aircraft structure depending on the actual flight conditions. Exemplarily, the wingtip arrangement 6 is shown in flight.
[0046] Exemplarily, the wing element 14 is arranged on the underside of the transition region 10 and extends in the spanwise direction, thereby resulting in an increase in the span. As indicated by the dotted line, the wing 14 is rotatable about an axis of rotation 16, which will be described in further...
PUM
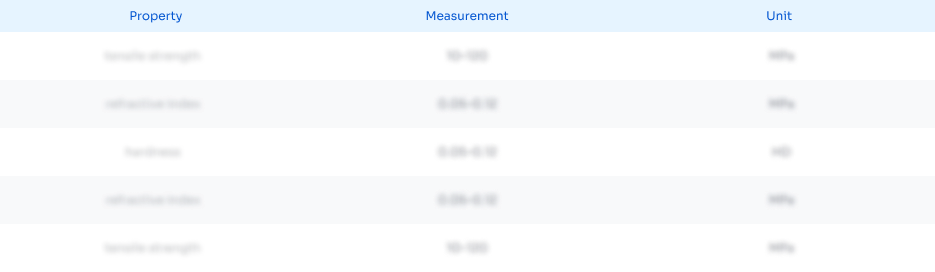
Abstract
Description
Claims
Application Information

- R&D
- Intellectual Property
- Life Sciences
- Materials
- Tech Scout
- Unparalleled Data Quality
- Higher Quality Content
- 60% Fewer Hallucinations
Browse by: Latest US Patents, China's latest patents, Technical Efficacy Thesaurus, Application Domain, Technology Topic, Popular Technical Reports.
© 2025 PatSnap. All rights reserved.Legal|Privacy policy|Modern Slavery Act Transparency Statement|Sitemap|About US| Contact US: help@patsnap.com