Compound temperature control system with combination of spacecraft feedback control and feedforward compensation
A technology of feedback control and temperature control system, applied in the direction of control/regulation system, temperature control, non-electric variable control, etc., can solve the problems of temperature control accuracy error, shrinkage, temperature control accuracy reduction, etc., to achieve precise temperature control, The effect of reducing the impact
- Summary
- Abstract
- Description
- Claims
- Application Information
AI Technical Summary
Problems solved by technology
Method used
Image
Examples
Embodiment
[0068] Such as figure 1 As shown, the composite temperature control system includes: temperature deviation feedback module, external heat flow and internal heat source feed-forward module, electric heating drive module, temperature measurement sensor and thermal control implementation module. Wherein, the temperature measuring sensor is implemented by using a thermistor or a thermocouple. In this embodiment, the temperature measuring sensor adopts a MF61 type thermistor, and the thermal control implementation module adopts an electric heating chip.
[0069] The thermistor MF61 is sensitive to the real-time temperature of the target temperature to be controlled, and provides it to the temperature measurement module in the temperature deviation feedback module; if the target temperature is 20°C, the measured temperature of the thermistor MF61 sensitive target temperature to be controlled is 18.15°C.
[0070] Based on this, the cycle calculation of the temperature control cycle a...
PUM
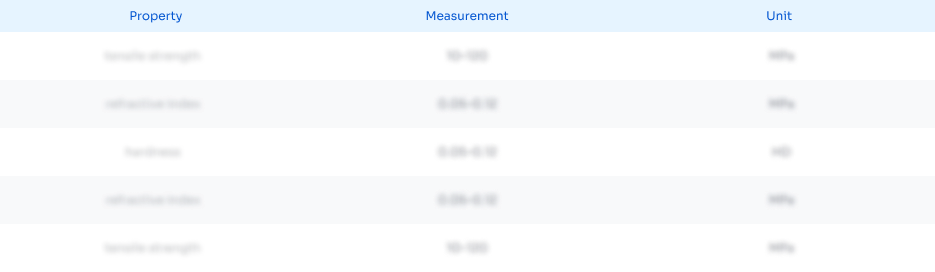
Abstract
Description
Claims
Application Information

- Generate Ideas
- Intellectual Property
- Life Sciences
- Materials
- Tech Scout
- Unparalleled Data Quality
- Higher Quality Content
- 60% Fewer Hallucinations
Browse by: Latest US Patents, China's latest patents, Technical Efficacy Thesaurus, Application Domain, Technology Topic, Popular Technical Reports.
© 2025 PatSnap. All rights reserved.Legal|Privacy policy|Modern Slavery Act Transparency Statement|Sitemap|About US| Contact US: help@patsnap.com