Differential supplementing device for metal powder bagging
A powder bagging and metal technology, which is applied in packaging, transportation and packaging, and the type of packaged items, can solve the problems of insufficient packaging bags, reduce the overflow rate of packaging bags, and low precision of powder blanking.
- Summary
- Abstract
- Description
- Claims
- Application Information
AI Technical Summary
Problems solved by technology
Method used
Image
Examples
Embodiment 1
[0023] refer to Figure 1 to Figure 6 As shown, the present invention is a differential compensation device for metal powder bagging, which includes a positioning transfer device 1 for packaging bag socketing, a filling mechanism 2 for filling metal powder in the packaging bag, and a A filling device 3 and a control device for making up the difference between the filled packaging bags. The positioning transfer device 1 includes several positioning jigs 11 for limiting the packaging bags and driving all the positioning tools. The jig 11 drives the electric cylinder 12 to move back and forth between the filling mechanism 2 and the filling device 3. The filling mechanism 2 includes a first drop hopper 21, which is used to control the discharge end of the first drop hopper 21. The disconnected solenoid valve 22 and the first shaking mechanism for shaking the first falling hopper 21, the first shaking mechanism is hinged with the middle section of the first falling hopper 21, and t...
Embodiment 2
[0031] refer to Figure 1 to Figure 6 As shown, the present invention is a differential compensation device for metal powder bagging, which includes a positioning transfer device 1 for packaging bag socketing, a filling mechanism 2 for filling metal powder in the packaging bag, and a A filling device 3 and a control device for making up the difference between the filled packaging bags. The positioning transfer device 1 includes several positioning jigs 11 for limiting the packaging bags and driving all the positioning tools. The jig 11 drives the electric cylinder 12 to move back and forth between the filling mechanism 2 and the filling device 3. The filling mechanism 2 includes a first drop hopper 21, which is used to control the discharge end of the first drop hopper 21. The disconnected solenoid valve 22 and the first shaking mechanism for shaking the first falling hopper 21, the first shaking mechanism is hinged with the middle section of the first falling hopper 21, and t...
PUM
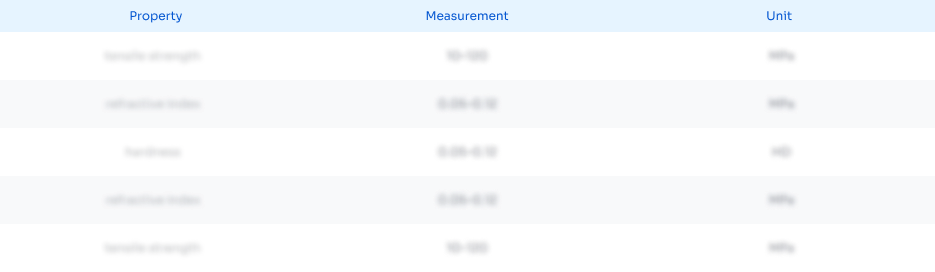
Abstract
Description
Claims
Application Information

- R&D
- Intellectual Property
- Life Sciences
- Materials
- Tech Scout
- Unparalleled Data Quality
- Higher Quality Content
- 60% Fewer Hallucinations
Browse by: Latest US Patents, China's latest patents, Technical Efficacy Thesaurus, Application Domain, Technology Topic, Popular Technical Reports.
© 2025 PatSnap. All rights reserved.Legal|Privacy policy|Modern Slavery Act Transparency Statement|Sitemap|About US| Contact US: help@patsnap.com