A Rotary Joint Variable Stiffness Actuator
A technology of rotating joints and variable stiffness, which is applied in the field of robotics, can solve the problems of small range of motion, high energy consumption of friction, and high energy consumption of stiffness adjustment, and achieve the effects of convenient control algorithm, low friction, and easy decoupling
- Summary
- Abstract
- Description
- Claims
- Application Information
AI Technical Summary
Problems solved by technology
Method used
Image
Examples
Embodiment Construction
[0027]The following will clearly and completely describe the technical solutions in the embodiments of the present invention with reference to the accompanying drawings in the embodiments of the present invention. Obviously, the described embodiments are only some, not all, embodiments of the present invention.
[0028] refer to Figure 1-6 , a rotary joint variable stiffness actuator, including a support base 5, the support base 5 includes a base 501, a housing 502 and two base connecting screws 503, the base 501 is located at the lower end of the housing 502, and the lower end of the housing 502 and the base The upper ends of 501 are in conflict, and one end of the two base connecting screws 503 runs through the base 501 and extends into the housing 502 for stable connection and easy disassembly. The housing 502 is provided with a torque output mechanism 1, and the torque output mechanism 1 is provided There are two output disk connection pins 102 parallel to each other, bot...
PUM
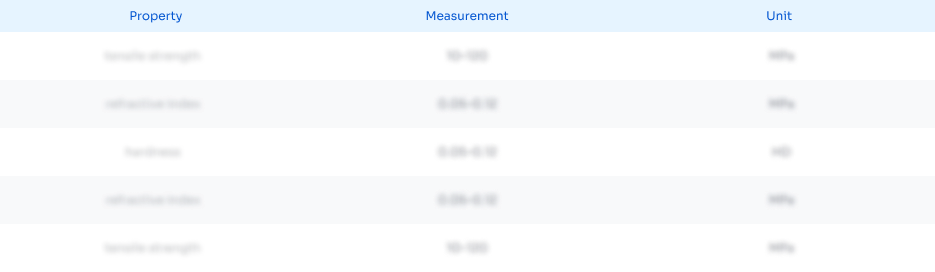
Abstract
Description
Claims
Application Information

- R&D Engineer
- R&D Manager
- IP Professional
- Industry Leading Data Capabilities
- Powerful AI technology
- Patent DNA Extraction
Browse by: Latest US Patents, China's latest patents, Technical Efficacy Thesaurus, Application Domain, Technology Topic, Popular Technical Reports.
© 2024 PatSnap. All rights reserved.Legal|Privacy policy|Modern Slavery Act Transparency Statement|Sitemap|About US| Contact US: help@patsnap.com