Natural rubber mastication method
A technology of natural rubber and rubber breaking, applied in the field of plasticizing of natural rubber, can solve the problems of poor dispersion coefficient of carbon black, uneven plasticizing of natural rubber, easy slippage, etc. The effect of plasticizing uniformity
- Summary
- Abstract
- Description
- Claims
- Application Information
AI Technical Summary
Problems solved by technology
Method used
Examples
Embodiment 1
[0024] (1) 140Kg of natural rubber and 10Kg of carbon black are dropped in the banbury mixer, carry out mastication, and described mastication pressure is 12Mpa, and mastication time is 320s;
[0025] (2) Take the natural rubber masticated in step (1), pass it through the isolation pool where the release agent is stored, then air-dry and collect the film, and park it for 5 hours to obtain the masticated natural rubber. Five plasticity tests were carried out, and the measured plasticity was 0.28-0.31.
[0026] (3) Put the plasticized natural rubber and synthetic rubber in step (2) into a 190L falling internal mixer, add suitable additives and continue mixing, the mixing pressure is 12Mpa, and the mixing time is 320s to obtain the mixing Glue, the measured dispersion coefficient of carbon black is 6.
Embodiment 2
[0028] (1) 140Kg of natural rubber and 15Kg of carbon black are dropped in the internal mixer, carry out mastication, and described mastication pressure is 12Mpa, and mastication time is 280s;
[0029] (2) Take the masticated natural rubber in step (1), pass it through the isolation pool where the release agent is stored, then air-dry and collect the film, and park it for 12 hours to obtain the masticated natural rubber. Five plasticity tests were carried out, and the measured plasticity was all 0.30.
[0030] (3) Put the plasticized natural rubber and synthetic rubber in step (2) into a 190L falling internal mixer, add suitable additives and continue mixing, the mixing pressure is 12Mpa, and the mixing time is 320s to obtain the mixing Glue, the measured dispersion coefficient of carbon black is 6.
Embodiment 3
[0032] (1) 140Kg of natural rubber and 20Kg of carbon black are dropped in the banbury mixer, carry out mastication, and described mastication pressure is 12Mpa, and mastication time is 240s;
[0033] (2) Take the masticated natural rubber in step (1), pass it through the isolation pool where the release agent is stored, then air-dry and collect the film, and park it for 36 hours to obtain the masticated natural rubber. Five plasticity tests were carried out, and the measured plasticity was 0.29-0.32.
[0034] (3) Put the plasticized natural rubber and synthetic rubber in step (2) into a 190L falling internal mixer, add suitable additives and continue mixing, the mixing pressure is 12Mpa, and the mixing time is 320s to obtain the mixing Glue, the measured dispersion coefficient of carbon black is 6.
PUM
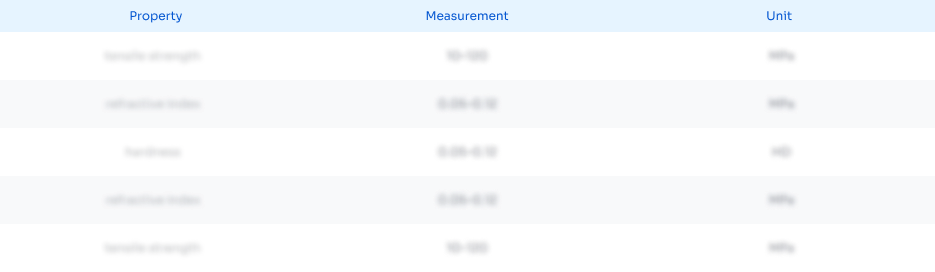
Abstract
Description
Claims
Application Information

- Generate Ideas
- Intellectual Property
- Life Sciences
- Materials
- Tech Scout
- Unparalleled Data Quality
- Higher Quality Content
- 60% Fewer Hallucinations
Browse by: Latest US Patents, China's latest patents, Technical Efficacy Thesaurus, Application Domain, Technology Topic, Popular Technical Reports.
© 2025 PatSnap. All rights reserved.Legal|Privacy policy|Modern Slavery Act Transparency Statement|Sitemap|About US| Contact US: help@patsnap.com