A direct drag teaching system and method based on a force sensor
A technology of drag teaching and force sensor, applied in the field of medical robots, which can solve the problems of inability to meet the needs of doctors' clinical operation, inflexibility, and large drag force.
- Summary
- Abstract
- Description
- Claims
- Application Information
AI Technical Summary
Problems solved by technology
Method used
Image
Examples
Embodiment Construction
[0061] In order to make the objectives, technical solutions and advantages of the embodiments of the present invention clearer, the following will clearly and completely describe the technical solutions in the embodiments of the present invention in conjunction with the accompanying drawings in the embodiments of the present invention. Obviously, the described embodiments It is a part of the embodiments of the present invention, not all the embodiments. Based on the embodiments of the present invention, all other embodiments obtained by those of ordinary skill in the art without creative work shall fall within the protection scope of the present invention.
[0062] An embodiment of the present invention provides a direct drag teaching system based on a force sensor, see figure 1 , The system includes: industrial computer 1, robot controller 2, robot 3, six-dimensional force sensor 4 and end effector 5;
[0063] The six-dimensional force sensor 4 is installed between the robot 2 an...
PUM
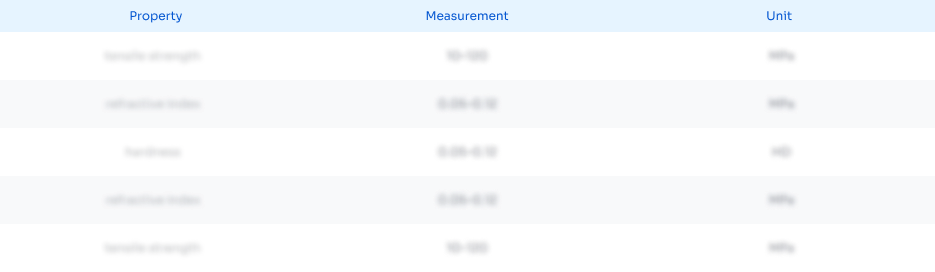
Abstract
Description
Claims
Application Information

- Generate Ideas
- Intellectual Property
- Life Sciences
- Materials
- Tech Scout
- Unparalleled Data Quality
- Higher Quality Content
- 60% Fewer Hallucinations
Browse by: Latest US Patents, China's latest patents, Technical Efficacy Thesaurus, Application Domain, Technology Topic, Popular Technical Reports.
© 2025 PatSnap. All rights reserved.Legal|Privacy policy|Modern Slavery Act Transparency Statement|Sitemap|About US| Contact US: help@patsnap.com