Assembling method of bearing assembly
An assembly method and technology of bearing components, which are applied to bearing components, shafts and bearings, mechanical equipment, etc., can solve problems such as bearing noise, reduced bearing service life, and bearing outer surface scars, and achieve timely protection of equipment and increased service life. , Excellent lubrication effect
- Summary
- Abstract
- Description
- Claims
- Application Information
AI Technical Summary
Problems solved by technology
Method used
Image
Examples
Embodiment Construction
[0025] use Figure 1-Figure 6 The structure of the self-lubricating dust-proof bearing according to one embodiment of the present invention will be described below.
[0026] Such as figure 1 and figure 2 As shown, the method for assembling a bearing assembly described in the present invention includes the following steps:
[0027] Step 1: Check whether the surface of the self-lubricating dust-proof bearing ball, inner ring, and outer ring is smooth;
[0028] Step 2: After the inspection of the self-lubricating bearing in step 1, clean the self-lubricating dust-proof bearing with gasoline or kerosene;
[0029] Step 3: After cleaning the self-lubricating bearing in step 2, heat it to 90-115 degrees with engine oil and quickly set it on the motor shaft;
[0030] Wherein, the self-lubricating dust-proof bearing described in step 1 includes an outer ring 1, an inner ring 2, balls 3, a lubricating module 4, a dust cover 5 and a dust-proof pad 6, and the outer ring 1 and the inn...
PUM
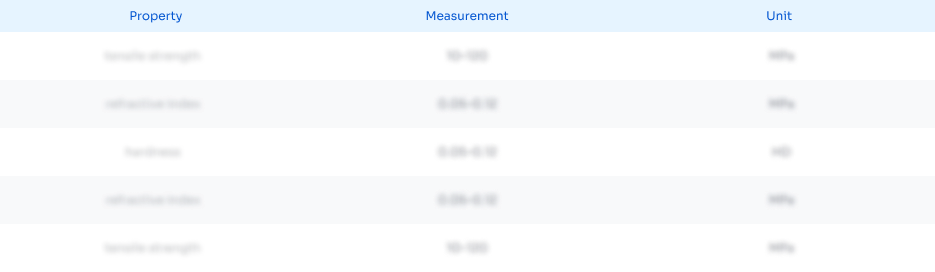
Abstract
Description
Claims
Application Information

- R&D
- Intellectual Property
- Life Sciences
- Materials
- Tech Scout
- Unparalleled Data Quality
- Higher Quality Content
- 60% Fewer Hallucinations
Browse by: Latest US Patents, China's latest patents, Technical Efficacy Thesaurus, Application Domain, Technology Topic, Popular Technical Reports.
© 2025 PatSnap. All rights reserved.Legal|Privacy policy|Modern Slavery Act Transparency Statement|Sitemap|About US| Contact US: help@patsnap.com