High-stiffness high-damping axial passive magnetic bearing with magnetic circuit decoupling function
A high-rigidity, high-damping technology, applied in the direction of shafts and bearings, bearings, anti-centrifugal force rotating parts, etc., can solve the problems of non-closed magnetic circuits, small support stiffness and damping, and optimized design of high stiffness to achieve improved uniformity The effect of reducing magnetic flux leakage and improving the utilization rate of magnetic flux
- Summary
- Abstract
- Description
- Claims
- Application Information
AI Technical Summary
Problems solved by technology
Method used
Image
Examples
specific Embodiment approach
[0014] The preferred embodiment of the high stiffness and high damping axial passive magnetic bearing with magnetic circuit decoupling of the present invention is as follows:
[0015]It is mainly composed of stator system and rotor system. The stator system mainly includes: outer mounting sleeve, outer magnetic ring, outer upper magnetic isolation ring, outer lower magnetic isolation ring, outer upper radial magnetization magnet steel, outer lower radial magnetization Magnetic steel, outer middle radial magnetic steel, outer middle upper magnetic ring, outer middle lower magnetic ring, outer upper axial magnetic steel, outer lower axial magnetic steel, outer middle upper axial Magnetic steel, outer, middle and lower axially magnetized magnetic steel, outer upper paramagnetic ring, outer lower paramagnetic ring, outer middle paramagnetic ring, outer magnetic steel lock nut, fixing seat, outer component lock nut, inner installation sleeve, Inner magnetic ring, inner upper magnet...
specific Embodiment
[0021] Such as figure 1 , 2As shown, the high-stiffness and high-damping axial passive magnetic bearing with magnetic circuit decoupling is mainly composed of a stator system and a rotor system. Ring 3A, Outer and lower magnetic separation ring 3B, Outer and upper radial magnetization magnet 4A, Outer and lower radial magnetization magnet 4B, Outer and middle radial magnetization magnet 5, Outer and middle upper and outer magnetic separation ring 6A, Outer and middle Lower spacer magnet ring 6B, outer upper axial magnetization magnet 7A, outer lower axial magnetization magnet 7B, outer middle upper axial magnetization magnet 8A, outer middle lower axial magnetization magnet 8B, outer upper Paramagnetic ring 9A, outer lower paramagnetic ring 9B, outer middle paramagnetic ring 10, outer magnetic steel lock nut 11, fixing seat 12, outer component lock nut 13, inner mounting sleeve 14, inner magnetic guide ring 15, inner upper magnet Steel 16A, inner lower magnetic steel 16B, in...
PUM
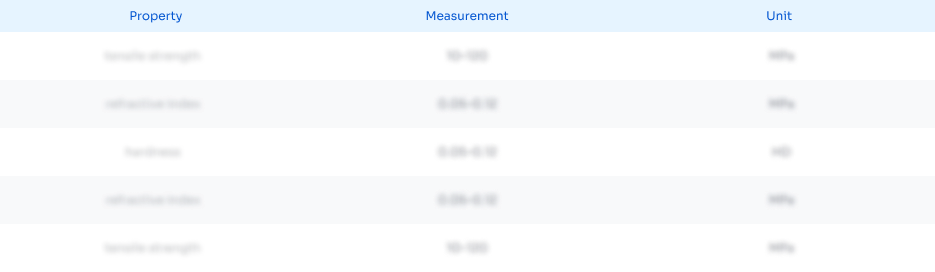
Abstract
Description
Claims
Application Information

- Generate Ideas
- Intellectual Property
- Life Sciences
- Materials
- Tech Scout
- Unparalleled Data Quality
- Higher Quality Content
- 60% Fewer Hallucinations
Browse by: Latest US Patents, China's latest patents, Technical Efficacy Thesaurus, Application Domain, Technology Topic, Popular Technical Reports.
© 2025 PatSnap. All rights reserved.Legal|Privacy policy|Modern Slavery Act Transparency Statement|Sitemap|About US| Contact US: help@patsnap.com