PCB circuit board printing process and production line thereof
A PCB circuit board, circuit board technology, applied in the printing process, printing, printing machine, etc., can solve the problems of reduced production efficiency, long drying time, heat waste of the dryer, etc., to protect the PCB board, and the processing process is tight Coherent, fast processing effect
- Summary
- Abstract
- Description
- Claims
- Application Information
AI Technical Summary
Problems solved by technology
Method used
Image
Examples
Embodiment Construction
[0023] The following will clearly and completely describe the technical solutions in the embodiments of the present invention. Obviously, the described embodiments are only some of the embodiments of the present invention, rather than all the embodiments. Based on the embodiments of the present invention, all other embodiments obtained by persons of ordinary skill in the art without making creative efforts belong to the protection scope of the present invention.
[0024] Specific embodiments of the present invention will be described below in conjunction with the accompanying drawings.
[0025] A PCB circuit board printing process, comprising, step 1: use mixed ink to print the A side of the circuit board; step 2: use UV light to dry the A side; step 3: turn over the circuit board; step 4: use Printing the B side of the circuit board with the mixed ink; step 5: drying the B side with a UV lamp; and step 6: drying the A side and the B side with a dryer.
[0026] Preferably, th...
PUM
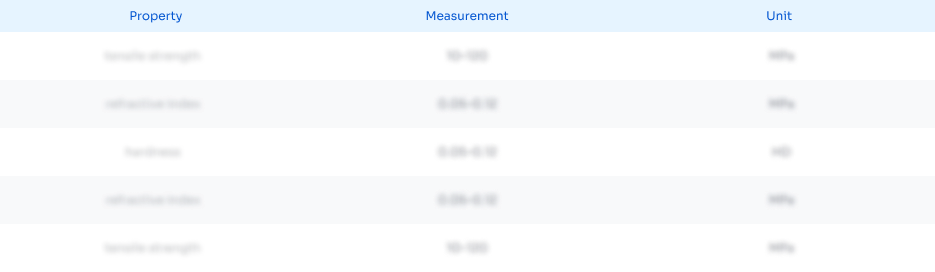
Abstract
Description
Claims
Application Information

- R&D Engineer
- R&D Manager
- IP Professional
- Industry Leading Data Capabilities
- Powerful AI technology
- Patent DNA Extraction
Browse by: Latest US Patents, China's latest patents, Technical Efficacy Thesaurus, Application Domain, Technology Topic, Popular Technical Reports.
© 2024 PatSnap. All rights reserved.Legal|Privacy policy|Modern Slavery Act Transparency Statement|Sitemap|About US| Contact US: help@patsnap.com