Dual motor position synchronous control strategy research design
A synchronous control, dual-motor technology, applied in the direction of speed adjustment of multiple motors, can solve the problems of impossible to ensure the accuracy of the intermediate transmission device, and the accuracy is difficult to achieve, and achieve the effect of high accuracy and good dynamic response.
- Summary
- Abstract
- Description
- Claims
- Application Information
AI Technical Summary
Problems solved by technology
Method used
Image
Examples
Embodiment Construction
[0022] In order to make the purpose and technical solutions of the embodiments of the present invention more clear, the technical solutions of the embodiments of the present invention will be clearly and completely described below in conjunction with the drawings of the embodiments of the present invention. Apparently, the described embodiments are some, not all, embodiments of the present invention. Based on the described embodiments of the present invention, all other embodiments obtained by persons of ordinary skill in the art without creative efforts shall fall within the protection scope of the present invention.
[0023] Such as figure 1 As shown, it is a schematic diagram of dual-motor load position synchronization control. The power supply system is DC power supply. The DC bus voltage is converted into AC power through the inverter and fed to the three-phase winding of the motor to supply power to the motor. The two motors drive the actuator respectively. Running, and...
PUM
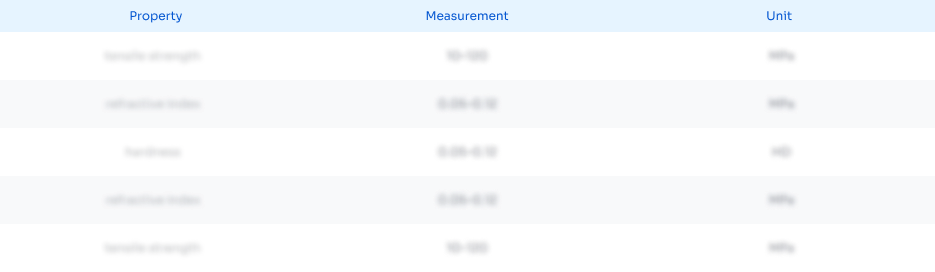
Abstract
Description
Claims
Application Information

- R&D
- Intellectual Property
- Life Sciences
- Materials
- Tech Scout
- Unparalleled Data Quality
- Higher Quality Content
- 60% Fewer Hallucinations
Browse by: Latest US Patents, China's latest patents, Technical Efficacy Thesaurus, Application Domain, Technology Topic, Popular Technical Reports.
© 2025 PatSnap. All rights reserved.Legal|Privacy policy|Modern Slavery Act Transparency Statement|Sitemap|About US| Contact US: help@patsnap.com