Sintering air volume control method
A technology of air volume control and air volume, which is applied in the direction of self-adaptive control, furnace control device, general control system, etc., can solve the problems of over-combustion of sintering ore, increase of sintering main exhaust fan, energy waste of main exhaust fan, etc., and achieve sintering production Stable, direct and effective control objects, and the effect of improving the quality of sintered ore
- Summary
- Abstract
- Description
- Claims
- Application Information
AI Technical Summary
Problems solved by technology
Method used
Image
Examples
Embodiment Construction
[0039] Taking the typical trolley-type sintering machine in China as an example, the present invention is described:
[0040] Detection of the present invention and hardware system see figure 1. The sintering mobile trolley contains the mixed raw materials being burned, and the lower part of the trolley is the fan system for extracting air to meet the combustion needs, mainly including sintering bellows, sintering flue and main exhaust fan. Since the trolley is spliced by a number of mobile independent trolleys, there are gaps and movable connections between the trolley and the trolley workshop, the bellows and the trolley workshop, which makes it easy to generate air leakage in various parts, and it is difficult to use effective means. Leak detection. The invention proposes to realize the online calculation of the air leakage rate by means of sound collection in the sintering workshop. As shown in the figure, several sound signal collectors are installed in the workshop ...
PUM
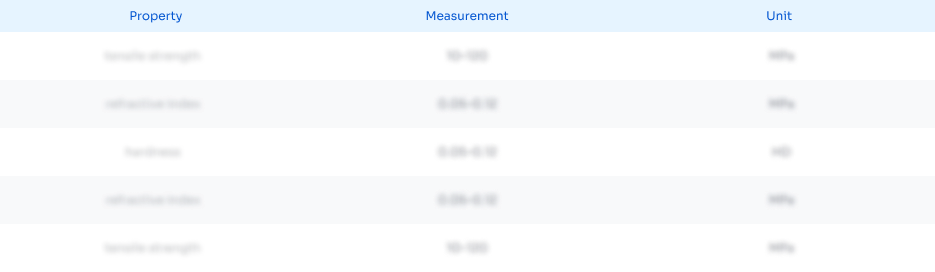
Abstract
Description
Claims
Application Information

- R&D Engineer
- R&D Manager
- IP Professional
- Industry Leading Data Capabilities
- Powerful AI technology
- Patent DNA Extraction
Browse by: Latest US Patents, China's latest patents, Technical Efficacy Thesaurus, Application Domain, Technology Topic, Popular Technical Reports.
© 2024 PatSnap. All rights reserved.Legal|Privacy policy|Modern Slavery Act Transparency Statement|Sitemap|About US| Contact US: help@patsnap.com