Specially-shaped plate crossbeam bridge steel spring supporting and jacking active reinforcing construction method
A technology of steel springs and special-shaped plates, which is applied in the field of active reinforcement construction method of steel spring abutments of bridge beams with special-shaped plates, can solve the problems of insufficient shear resistance and potential safety hazards of the middle beams, and achieve the effect of strengthening quality and ensuring reinforcement
- Summary
- Abstract
- Description
- Claims
- Application Information
AI Technical Summary
Problems solved by technology
Method used
Image
Examples
Embodiment 1
[0047] A construction method for actively reinforcing steel spring abutments of special-shaped plate beam bridges, mainly including the following steps:
[0048] Step S101: First, add π-shaped steel cap beams 3 on both sides of the pier column 2;
[0049] Step S102: Then set a force-measuring adjustable pot-type rubber bearing 4 at both ends of the π-shaped steel cover beam 3;
[0050] Step S103: Finally, use the synchronous hydraulic jacking system to support the beam and the π-shaped steel cover beam 3, so that the π-shaped steel cover beam 3 produces elastic deformation; when the stress and strain on the π-shaped steel cover beam 3 reach the standard, adjust The force-measuring adjustable basin-type rubber bearing 4 makes the upper and lower sides of the force-measuring adjustable basin-type rubber bearing 4 closely adhere to the middle beam 1 and the π-shaped steel cover beam 3 respectively, and the force-measuring adjustable basin-type rubber bearing 4 is locked, and aft...
Embodiment 2
[0052] This embodiment is further optimized on the basis of Embodiment 1. Before the construction, it also includes step A. The step A includes the following steps: excavate the periphery of the pier column 2, and expose the top surface of the cap; the pier column 2. The periphery of the platform cap is hardened with C20 concrete, and the thickness is 20cm to ensure the flatness of the base; the top surface of the platform is leveled with 2 cm thick 60MPa epoxy mortar. Through the operation of the step A, the present invention ensures the flatness of the bearing platform and the smooth progress of the follow-up work.
[0053] Other parts of this embodiment are the same as those of Embodiment 1, so details are not repeated here.
Embodiment 3
[0055] This embodiment is further optimized on the basis of embodiment 2, as Figure 1-Figure 5 As shown, the step S101 mainly includes the following steps:
[0056] Step S1011: Before installing the π-shaped steel cover beam 3, drill anchor bolt holes on the top surface of the bearing platform 7 in advance, and the drill holes are drilled with water drills, and the hole diameter is 35mm; Platform 7, anchor bolt model M30, length 80cm;
[0057] Step S1012: Assembling the π-shaped steel cover beam 3 is about to assemble the parts that are divided into four sections in the factory, that is, the two sections of beams on the upper part of the π-shaped steel cover beam 3 and the two steel piers 5 below. The two beams on the upper part of the shaped steel cover beam 3 are butted, and the pier column 2 is wrapped in the middle, and welded after alignment. After the welding is completed, the two steel pier columns 2 are placed on the π-shaped steel cover beam 3 respectively On the l...
PUM
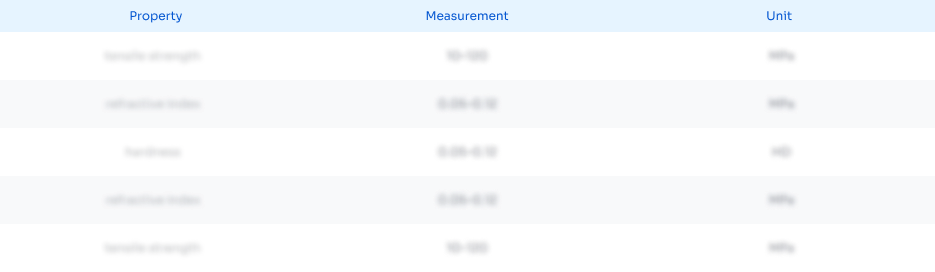
Abstract
Description
Claims
Application Information

- R&D
- Intellectual Property
- Life Sciences
- Materials
- Tech Scout
- Unparalleled Data Quality
- Higher Quality Content
- 60% Fewer Hallucinations
Browse by: Latest US Patents, China's latest patents, Technical Efficacy Thesaurus, Application Domain, Technology Topic, Popular Technical Reports.
© 2025 PatSnap. All rights reserved.Legal|Privacy policy|Modern Slavery Act Transparency Statement|Sitemap|About US| Contact US: help@patsnap.com