Liquid metal pressure-driven robotic joint self-generating device
A technology of robot joints and liquid metal, applied in the field of robots, can solve the problems of reduced speed, high working temperature, large external connection, etc., and achieve the effect of improving dynamic characteristics, excellent thermal conductivity, and high self-generating efficiency
- Summary
- Abstract
- Description
- Claims
- Application Information
AI Technical Summary
Problems solved by technology
Method used
Image
Examples
Embodiment
[0021] The liquid metal pressure-driven robot joint self-generating device of the embodiment of the present invention adopts the liquid metal pressure-driven robot leg joint self-generating device, and its working principle is shown in figure 1 , whose structure see figure 2, including: thermal temperature difference power generation type liquid metal pressure working cylinder 1, liquid metal magnetic fluid generator 2, servo valve 3, magnetic pump 4, robot joint 5, sensor 6, intelligent controller 7, one-way valve 8, filter 9 , overflow valve 10, liquid metal storage tank 11, supercapacitor 12; liquid metal magnetic fluid generator 2 is assembled on the liquid metal 29 inlet channel of thermal thermoelectric power generation type liquid metal pressure working cylinder 1, and constitutes a liquid metal pressure-driven robot Joint and self-generating functional structure; liquid metal 29 is stored in the liquid metal storage tank 11, which is connected to the filter 9; the fil...
PUM
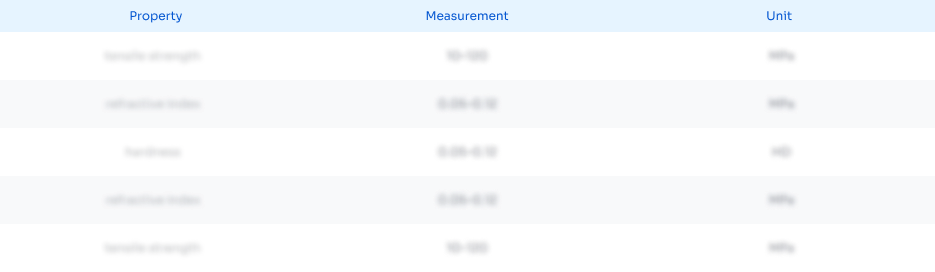
Abstract
Description
Claims
Application Information

- Generate Ideas
- Intellectual Property
- Life Sciences
- Materials
- Tech Scout
- Unparalleled Data Quality
- Higher Quality Content
- 60% Fewer Hallucinations
Browse by: Latest US Patents, China's latest patents, Technical Efficacy Thesaurus, Application Domain, Technology Topic, Popular Technical Reports.
© 2025 PatSnap. All rights reserved.Legal|Privacy policy|Modern Slavery Act Transparency Statement|Sitemap|About US| Contact US: help@patsnap.com