Bearing gland at end of submersible pump rotor shaft
A technology for bearing glands and rotor shafts, which is applied to components, pumps, pump devices, etc. of pumping devices for elastic fluids. It can solve the problems of high loss costs, bearing wear, and damage to motors, and avoid mutual scratches. The effect of reducing maintenance cost and prolonging service life
- Summary
- Abstract
- Description
- Claims
- Application Information
AI Technical Summary
Problems solved by technology
Method used
Image
Examples
Embodiment Construction
[0012] A bearing gland at the rotor shaft end of a submersible pump according to the present invention will be further described below in conjunction with the accompanying drawings and specific embodiments:
[0013] figure 1 It is a structural schematic diagram of the bearing gland at the shaft end of the original submersible pump rotor. In the figure, the bottom end 3 of the bearing gland 2 has only a thinner wall thickness, which cannot provide auxiliary support for the rotor 4 axis. Furthermore, in some sediments In a large groundwater environment, the fine sand particles will cause great wear to the bearing 1. Once the bearing 1 is damaged and the gap increases, the rotor 4 will swing. Since the gap between the rotor 4 and the stator 5 is small, the rotor 4 Once it swings, the rotor 4 and the stator 5 will rub against each other, thereby damaging the motor.
[0014] figure 2 It is a structural schematic diagram of the bearing gland at the rotor shaft end of the submersi...
PUM
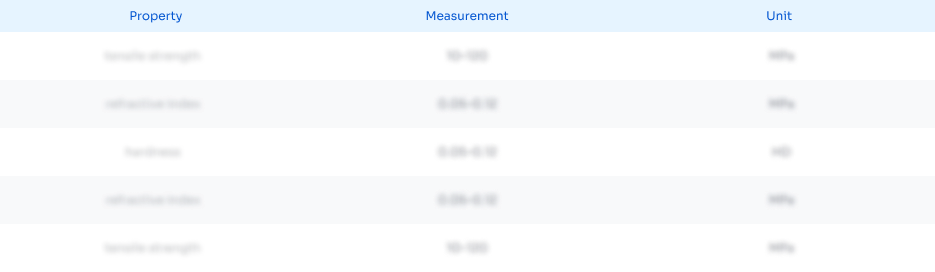
Abstract
Description
Claims
Application Information

- Generate Ideas
- Intellectual Property
- Life Sciences
- Materials
- Tech Scout
- Unparalleled Data Quality
- Higher Quality Content
- 60% Fewer Hallucinations
Browse by: Latest US Patents, China's latest patents, Technical Efficacy Thesaurus, Application Domain, Technology Topic, Popular Technical Reports.
© 2025 PatSnap. All rights reserved.Legal|Privacy policy|Modern Slavery Act Transparency Statement|Sitemap|About US| Contact US: help@patsnap.com