Sintering waste heat power generation system waste heat recovery device and application method thereof
A waste heat recovery device and waste heat power generation technology, which is applied in the field of boiler waste heat recovery, can solve problems such as poor waste heat recovery power generation effect, poor waste heat recovery effect, unreasonable design and operation mode of waste heat recovery system, etc., to increase power generation and increase The effect of waste heat recovery and the effect of reducing self-consumption rate
- Summary
- Abstract
- Description
- Claims
- Application Information
AI Technical Summary
Problems solved by technology
Method used
Image
Examples
Embodiment Construction
[0023] In order to make the object, technical solution and advantages of the present invention clearer, the implementation manner of the present invention will be further described in detail below in conjunction with the accompanying drawings.
[0024] see figure 1 , a waste heat recovery device for sintering waste heat power generation system, which has:
[0025] The waste heat boiler is provided with a high-temperature flue gas inlet, a low-temperature flue gas inlet and a flue gas outlet;
[0026] A ring cooler, which includes a high temperature section of the ring cooler and a low temperature section of the ring cooler;
[0027] The gas collecting air hood is set on the ring cooler;
[0028] The high-temperature intake smoke pipe, the first end is connected to the gas collecting hood of the high-temperature section of the ring cooler, and the second end is connected to the high-temperature flue gas inlet;
[0029] The low-temperature air intake pipe, the first end is co...
PUM
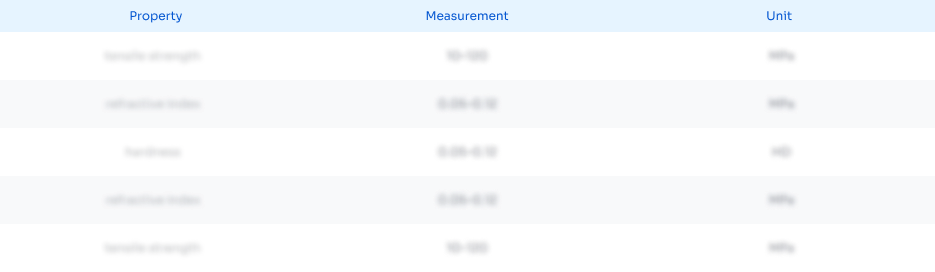
Abstract
Description
Claims
Application Information

- Generate Ideas
- Intellectual Property
- Life Sciences
- Materials
- Tech Scout
- Unparalleled Data Quality
- Higher Quality Content
- 60% Fewer Hallucinations
Browse by: Latest US Patents, China's latest patents, Technical Efficacy Thesaurus, Application Domain, Technology Topic, Popular Technical Reports.
© 2025 PatSnap. All rights reserved.Legal|Privacy policy|Modern Slavery Act Transparency Statement|Sitemap|About US| Contact US: help@patsnap.com