Rock breaking device
A technology of rock breaking device and traveling device, which is applied to earth moving machines/shovels, earthwork drilling and cutting machines, etc., can solve the problems of large momentum loss, increase the thrust of the oil cylinder, influence the torque, etc. Reduced force, improved rigidity transmission capability, and large torque adjustment range
- Summary
- Abstract
- Description
- Claims
- Application Information
AI Technical Summary
Problems solved by technology
Method used
Image
Examples
Embodiment 1
[0053] A rock-breaking device mounted on an excavator, comprising a large arm 2, a small arm 3 ripper 6, a stick cylinder 4, a ripper cylinder 5, and bucket teeth 7. The excavator has an upper body and a lower traveling device, The upper vehicle body is rotatably connected to the lower traveling device. One end of the boom 2 is hinged to the upper body of the excavator, and the other end is hinged to the small arm 3 through the first hinge shaft 34. One end of the boom cylinder is hinged to the upper vehicle body, and the other end is hinged to the The boom is hinged through the second hinge shaft 29, one end of the arm cylinder 4 is hinged with the upper middle of the boom through the third hinge shaft 28, and the other end is hinged with the upper end of the small arm 3 through the fourth hinge shaft 42, and the upper end of the small arm 3 is connected by The fifth hinge shaft 55 is hinged with one end of the ripper cylinder 5, the other end of the ripper cylinder 5 is hinge...
Embodiment 2
[0064] The weight of the ripper is 10.37 tons, and the weight of the ripper is 61% of the total weight of the rock breaking device.
[0065] There are 2 positions for the 4th hinge axis, 3 positions for the 5th hinge axis, and 3 positions for the 6th hinge axis.
[0066] Line 73 divides the ripper into upper and lower parts. After calculation, the weight of the lower part is 1.07 tons and the volume is 0.137 cubic meters. The weight of the upper part is 9.3 tons and the volume is 1.19 cubic meters. The weight of the upper part is 8.7 times the weight of the lower part.
[0067] The jib weighs 2 tons and has a volume of 0.52 cubic meters.
[0068] Ripper 6 does not have a hollow cavity.
[0069] When the ripper cylinder 5 is installed at the minimum angle of the included angle C, when the ripper cylinder is fully retracted, the included angle C is 24 degrees, and the vertical distance from the axis of the ripper cylinder 5 to the hinge shaft 63 is 1040 mm, and the hinge shaft 63...
Embodiment 3
[0077] The weight of the ripper is 14.45 tons, and the weight of the ripper is 85% of the total weight of the rock breaking device.
[0078] There are 2 positions on the 4th hinge axis, 3 positions on the 5th hinge axis, 4 positions on the 6th hinge axis, and 1 position on the 7th hinge axis.
[0079] Line 73 divides the ripper into upper and lower parts, the lower part weighs 0.9 tons and has a volume of 0.115 cubic meters, and the upper part weighs 13.55 tons and has a volume of 1.74 cubic meters, and the weight of the upper part is 15 times the weight of the lower part.
[0080] When the ripper cylinder 5 is installed at the maximum angle of the included angle C, when the ripper cylinder is fully retracted, the included angle C is 143 degrees, and the vertical distance from the axis of the ripper cylinder 5 to the hinge shaft 63 is 892 mm, and the hinge shaft 63 to the lower end The distance of 72 is 1775 mm, the ratio of power arm to resistance arm is 0.5, the maximum dist...
PUM
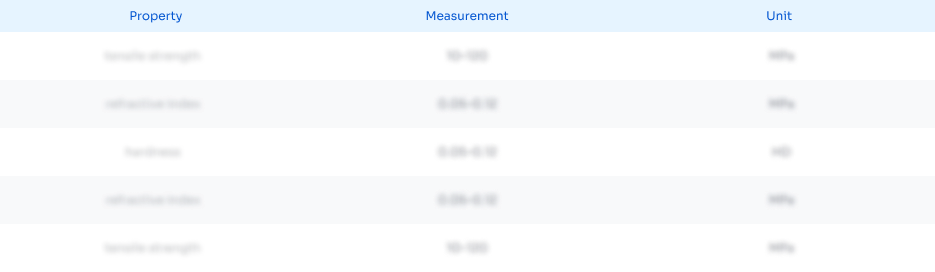
Abstract
Description
Claims
Application Information

- R&D
- Intellectual Property
- Life Sciences
- Materials
- Tech Scout
- Unparalleled Data Quality
- Higher Quality Content
- 60% Fewer Hallucinations
Browse by: Latest US Patents, China's latest patents, Technical Efficacy Thesaurus, Application Domain, Technology Topic, Popular Technical Reports.
© 2025 PatSnap. All rights reserved.Legal|Privacy policy|Modern Slavery Act Transparency Statement|Sitemap|About US| Contact US: help@patsnap.com