Robot modular assemble mechanical arm
A modular, robotic arm technology, applied in the field of robotic arms, can solve the problems of narrow range of use of robotic arms, high maintenance and replacement costs, and limited use of areas, to facilitate transportation and storage, save replacement materials and costs, and versatility strong effect
- Summary
- Abstract
- Description
- Claims
- Application Information
AI Technical Summary
Problems solved by technology
Method used
Image
Examples
Embodiment 1
[0024] Such as Figure 1~2As shown, a robot modular assembly mechanical arm of the present invention includes an arm body, and the arm body includes a plurality of interconnected arm sections 1, and each section arm section 1 includes a rectangular block 2, on opposite sides of the rectangular block 2 One end is respectively provided with a bump 3, and one of the bumps 3 is fixed with a fixed shaft 4, and one end of the fixed shaft 4 is provided with a driving installation hole 5 communicating with the outside world, and the other end is provided with a fixing hole 6, and in the fixing hole The inner wall of 6 is provided with at least one annular groove 7 and chute 8, one end of said chute 8 communicates with the annular groove 7, the other end is flush with the mouth of the fixing hole 6, and a moving shaft is arranged in the other protruding block 3 9. One end of the moving shaft 9 protrudes from the surface of the bump 3, and the protruding end matches the fixing hole 6 an...
Embodiment 2
[0028] Such as Figure 1~2 As shown, on the basis of Embodiment 1, the end of the fixed shaft 4 or the moving shaft 9 having the drive installation hole 5 is a spherical body, and the diameter of the spherical body is 1.25 of the diameter of the wall of the fixed shaft 4 or the moving shaft 9. ~1.55 times. The above structure can effectively prevent the fixed shaft and the moving shaft from falling off from their respective protrusions; Disperse the external axial stress on the rotor, reduce the radial deformation of the connecting section of the rotor, and improve the service life of the fixed and moving shafts.
[0029] In addition, the inventor tested the relationship between the diameter of the spherical end of the rotor and the radial deformation of the rotor, and applied an axial stress test of 170MP to the rotor. Some test results are as follows:
[0030]
[0031] From the table above, it can be seen that if the diameter of the spherical body is designed to be 1.25...
Embodiment 3
[0033] Such as Figure 1~3 As shown, on the basis of Embodiment 1, a positioning rod 12 is also provided on the bump 3 where the fixed rotating shaft 4 is located, and an annular positioning groove 13 is also opened on the convex block 3 where the moving rotating shaft 9 is located. The centerline coincides with the central axis of the moving shaft 9, and the annular positioning groove 13 is filled with lubricating oil. There are several threaded holes 14 on the bottom surface of the annular positioning groove 13, and the threaded holes 14 are equidistantly arranged around the centerline of the annular positioning groove 13, and also include two stop screws 15, the diameter of the stop screw 15 is the same as that of the ring. The inner diameters of the positioning grooves 13 are equally large. The above structure helps the fixed shaft 4 and the moving shaft 6 to be aligned and connected, and limits the position after the fixed shaft 4 and the moving shaft 6 are connected. m...
PUM
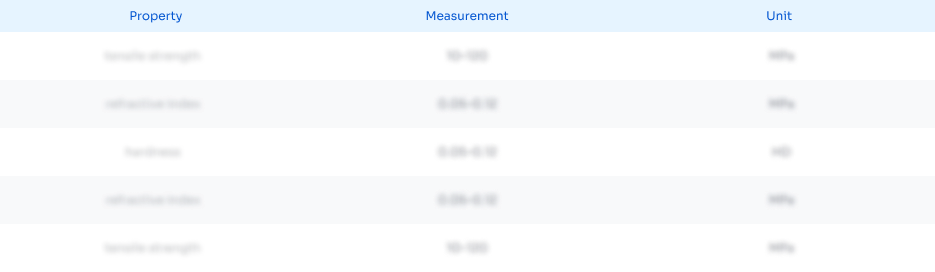
Abstract
Description
Claims
Application Information

- R&D
- Intellectual Property
- Life Sciences
- Materials
- Tech Scout
- Unparalleled Data Quality
- Higher Quality Content
- 60% Fewer Hallucinations
Browse by: Latest US Patents, China's latest patents, Technical Efficacy Thesaurus, Application Domain, Technology Topic, Popular Technical Reports.
© 2025 PatSnap. All rights reserved.Legal|Privacy policy|Modern Slavery Act Transparency Statement|Sitemap|About US| Contact US: help@patsnap.com