Manipulator joint absolute angle measuring method without encoder
A technology that does not require coding and measurement methods. It is applied in the field of robotics and can solve the problem of measuring the absolute angle of joints in small manipulator joints. It can prevent stalling or lost steps, reduce costs, and ensure continuous rotation.
- Summary
- Abstract
- Description
- Claims
- Application Information
AI Technical Summary
Problems solved by technology
Method used
Image
Examples
Embodiment 1
[0040] Based on the linkage structure of the above-mentioned manipulator joints, the method for measuring the absolute angle of the manipulator joints without an encoder for the first time includes the following implementation steps:
[0041] S1: Calibrate the joints of the manipulator, the pressure sensor 10 and the stepping motor 1 used for the first time, and obtain the initial angle value of the joints of the manipulator and the reading of the pressure sensor 10 when the stepping motor 1 is locked;
[0042] S2: Determine the stepping angle of the stepping motor 1, denoted as α;
[0043] S3: The output end of the stepping motor 1 is connected to the input end of the reduction mechanism 2, and the reduction ratio between the stepping motor 1 and the reduction mechanism 2 is determined, which is denoted as k;
[0044] S4: install the worm 71 on the output shaft of the reduction mechanism 2, install the worm / helical gear 72 on the second fixed plate 41 of the joint rear end se...
Embodiment 2
[0055] Based on the linkage structure of the manipulator joints mentioned above, the absolute angle measurement method for the non-encoder-free manipulator joints that is not used for the first time includes the following implementation steps:
[0056] S1: The main control chip 6 initializes the joint angle of the manipulator, that is, reads the relative motion angle value of the manipulator joint when the stepper motor 1 in the fixed address was powered off last time;
[0057] S2: Immediately after the main control chip 6 completes the joint angle initialization, the data in the fixed address is erased, and the main control chip 6 is always in a writable state;
[0058] S3: Calibrate the pressure sensor 10 and the stepping motor 1 to obtain the reading of the pressure sensor 10 when the stepping motor 1 is locked;
[0059] S4: Determine the stepping angle of the stepping motor 1, denoted as α;
[0060] S5: The output end of the stepping motor 1 is connected to the input end ...
PUM
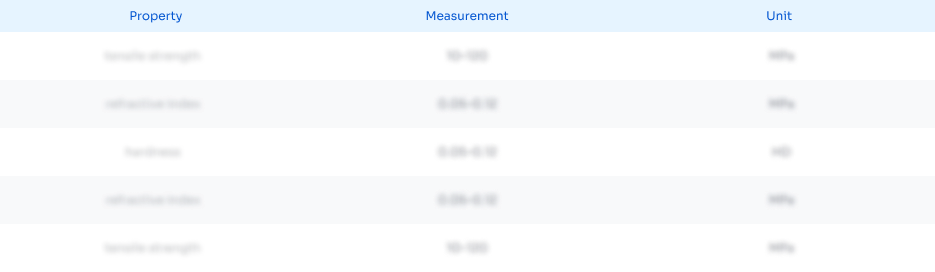
Abstract
Description
Claims
Application Information

- R&D Engineer
- R&D Manager
- IP Professional
- Industry Leading Data Capabilities
- Powerful AI technology
- Patent DNA Extraction
Browse by: Latest US Patents, China's latest patents, Technical Efficacy Thesaurus, Application Domain, Technology Topic, Popular Technical Reports.
© 2024 PatSnap. All rights reserved.Legal|Privacy policy|Modern Slavery Act Transparency Statement|Sitemap|About US| Contact US: help@patsnap.com