An autonomous take-off control system and method for a flapping-wing aircraft
A flapping-wing aircraft and control system technology, applied in the field of flapping-wing aircraft, can solve problems such as involuntary take-off, and achieve the effects of reducing power, improving efficiency, and compact structure
- Summary
- Abstract
- Description
- Claims
- Application Information
AI Technical Summary
Problems solved by technology
Method used
Image
Examples
no. 1 example
[0064] This embodiment provides an autonomous take-off assisting system for a flapping-wing aircraft, figure 1 It is a structural schematic diagram of the autonomous take-off auxiliary system of the flapping-wing aircraft in this embodiment. Such as figure 1 As shown, the autonomous take-off auxiliary system of the flapping wing aircraft described in this embodiment includes: remote control car 1, support 2, strain measuring device 3, vehicle speed measuring device 4, vehicle-mounted control board 5, airborne control board 6 ( figure 1 not shown in); among them,
[0065] The remote control car 1 is used to carry a support 2 , a strain measuring device 3 , a vehicle speed measuring device 4 , and a vehicle control panel 5 . figure 2 Shown is a schematic structural diagram of the remote control car described in this embodiment. Such as figure 2 As shown, the remote control car 1 has four installation holes a, b, c, d. In the actual preparation process, the remote control ...
no. 2 example
[0083] This embodiment provides a control system for autonomous take-off of a flapping-wing aircraft, Figure 7 Shown is a schematic structural diagram of the autonomous take-off control system of the flapping-wing aircraft in this embodiment. Such as Figure 7 As shown, the autonomous take-off control system of the flapping-wing aircraft in this embodiment includes the autonomous take-off assisting system of the flapping-wing aircraft in the first embodiment, and also includes: a remote controller, a wireless receiver, the flapping-wing aircraft, and an attitude sensor. The wireless receiver here can be mounted on the remote control car for wireless communication with the remote control. The airborne control board is installed on the flapping-wing aircraft; the attitude sensor is installed on the flapping-wing aircraft.
[0084] Figure 8 Shown is a schematic diagram of the working principle of the autonomous take-off control system of the flapping-wing aircraft in this em...
no. 3 example
[0086] This embodiment provides a control method for autonomous take-off of a flapping-wing aircraft, said method is realized based on the control system for autonomous take-off of the flapping-wing aircraft described in the second embodiment, Figure 9 It is a schematic flow chart of the autonomous take-off control method of the flapping-wing aircraft in this embodiment. Such as Figure 9 As shown, the autonomous take-off control method of the flapping wing aircraft of the present embodiment comprises the following steps:
[0087] Step S1, fix the flapping-wing aircraft on the remote control car, and preset the vehicle speed threshold for autonomous take-off and start of the flapping-wing aircraft.
[0088] Preferably, in this step, fixing the flapping-wing aircraft on the remote control car is further as follows:
[0089] The flapping wing aircraft is fixed on the beam of the remote control car through the magnetism generated by electrifying the electromagnet, and the comm...
PUM
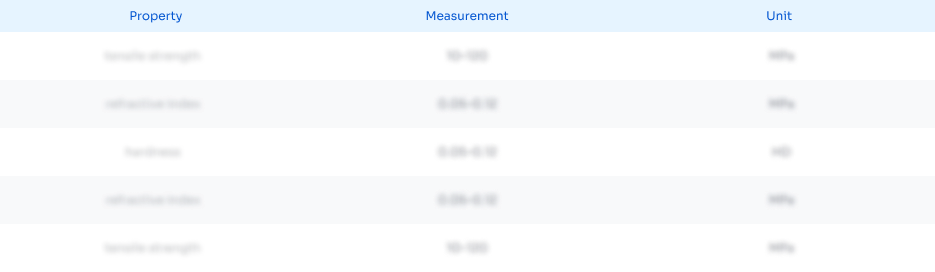
Abstract
Description
Claims
Application Information

- R&D Engineer
- R&D Manager
- IP Professional
- Industry Leading Data Capabilities
- Powerful AI technology
- Patent DNA Extraction
Browse by: Latest US Patents, China's latest patents, Technical Efficacy Thesaurus, Application Domain, Technology Topic, Popular Technical Reports.
© 2024 PatSnap. All rights reserved.Legal|Privacy policy|Modern Slavery Act Transparency Statement|Sitemap|About US| Contact US: help@patsnap.com