A kind of automatic guide rail carrying device and robot cooperative carrying method and system
A mobile robot, robot technology, applied in machine learning, control/regulation systems, instruments, etc., can solve problems such as failure of transportation tasks, reduced transportation efficiency, and robots unable to continue to work
- Summary
- Abstract
- Description
- Claims
- Application Information
AI Technical Summary
Problems solved by technology
Method used
Image
Examples
Embodiment Construction
[0083] The present invention will be further described below in conjunction with the accompanying drawings and embodiments.
[0084] like figure 1 As shown, an automatic guide rail carrying device and a robot cooperative carrying method, comprising the following steps:
[0085] Step 1: Set up a ground guide rail between the workbenches where the starting point and end point of the transportation are located, set up a desktop guideway on the workbench, a designated pick-up location, a temporary pick-up location, and a designated place to put the object, and use the remote controller to send the pick-up instruction;
[0086] Use the remote controller to send fetching instructions to the mobile robot and the desktop controller, so that the mobile robot moves to the fetching workbench, and the desktop robot moves to the designated pick-up position to start the fetching task;
[0087] The desktop guide rail is arranged in the middle of the workbench, and the designated pick-up po...
PUM
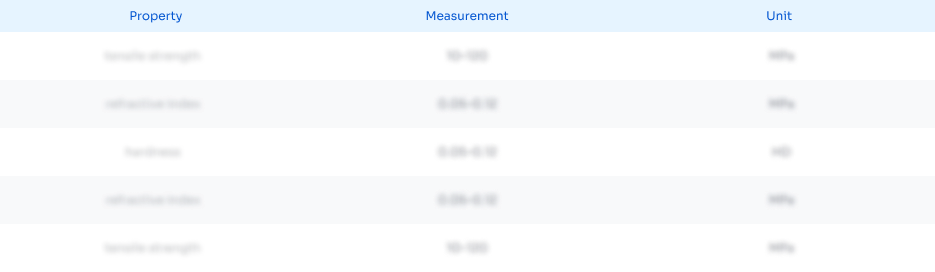
Abstract
Description
Claims
Application Information

- R&D
- Intellectual Property
- Life Sciences
- Materials
- Tech Scout
- Unparalleled Data Quality
- Higher Quality Content
- 60% Fewer Hallucinations
Browse by: Latest US Patents, China's latest patents, Technical Efficacy Thesaurus, Application Domain, Technology Topic, Popular Technical Reports.
© 2025 PatSnap. All rights reserved.Legal|Privacy policy|Modern Slavery Act Transparency Statement|Sitemap|About US| Contact US: help@patsnap.com