Coaxial optical dual-camera splicing structure
An optical camera and dual-camera technology, applied in the field of aerospace optical remote sensors, can solve the problems of large camera position changes, complicated installation procedures, and difficulty in ensuring accuracy, and achieve strong versatility, wide application range, and high pointing accuracy in orbit Effect
- Summary
- Abstract
- Description
- Claims
- Application Information
AI Technical Summary
Problems solved by technology
Method used
Image
Examples
Embodiment Construction
[0038] In order to make the solution of the present invention clearer, the present invention will be further described below in conjunction with the accompanying drawings and specific embodiments:
[0039] Such as figure 1 As shown, a coaxial optical dual-camera splicing structure includes: a camera connecting plate 3, a cylindrical pin 4, a main load-bearing structure 5, and a supporting structure 6;
[0040] The camera A1 and the camera B2 are connected to the camera connection plate 3 with screws through their respective main load-bearing structures 5 , and are positioned by cylindrical pins 4 . Finally, the dual cameras are connected to the support structure 6 after being assembled. There is a certain angle between the optical axes of camera A1 and camera B2, such as figure 2 As shown, the angle is measured at the early stage of structure assembly and adjusted in real time. After the adjustment is in place, the cylindrical pin 4 is prepared, and the subsequent two camer...
PUM
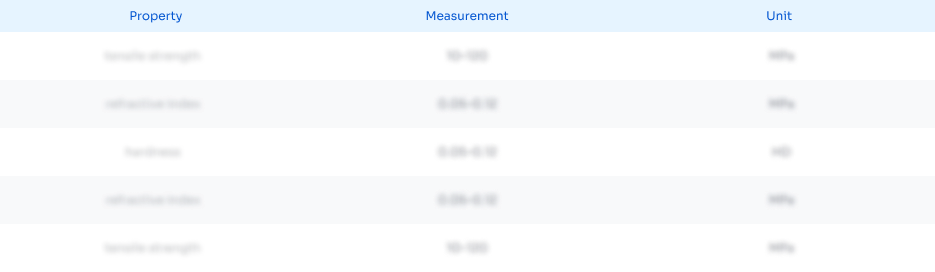
Abstract
Description
Claims
Application Information

- R&D
- Intellectual Property
- Life Sciences
- Materials
- Tech Scout
- Unparalleled Data Quality
- Higher Quality Content
- 60% Fewer Hallucinations
Browse by: Latest US Patents, China's latest patents, Technical Efficacy Thesaurus, Application Domain, Technology Topic, Popular Technical Reports.
© 2025 PatSnap. All rights reserved.Legal|Privacy policy|Modern Slavery Act Transparency Statement|Sitemap|About US| Contact US: help@patsnap.com