Calibration method of automatic optical detection device, and automatic repairing system
An automatic optical detection and calibration method technology, which is applied in the direction of optical testing flaws/defects, etc., can solve problems such as unguaranteed, low calibration accuracy, and inability to be absolutely guaranteed
- Summary
- Abstract
- Description
- Claims
- Application Information
AI Technical Summary
Problems solved by technology
Method used
Image
Examples
Embodiment Construction
[0049] Reference will now be made in detail to the exemplary embodiments, examples of which are illustrated in the accompanying drawings. When the following description refers to the accompanying drawings, the same numerals in different drawings refer to the same or similar elements unless otherwise indicated. The implementations described in the following exemplary examples do not represent all implementations consistent with the present invention. Rather, they are merely examples of apparatuses and methods consistent with aspects of the invention as recited in the appended claims.
[0050] Before introducing the calibration method of the automatic optical inspection equipment and the automatic repair system in the embodiment of the present invention, the automatic repair system in the related art is briefly introduced.
[0051] In the related art, the automatic repair system includes automatic optical inspection equipment (AOI) and repair equipment (repair). Taking the repai...
PUM
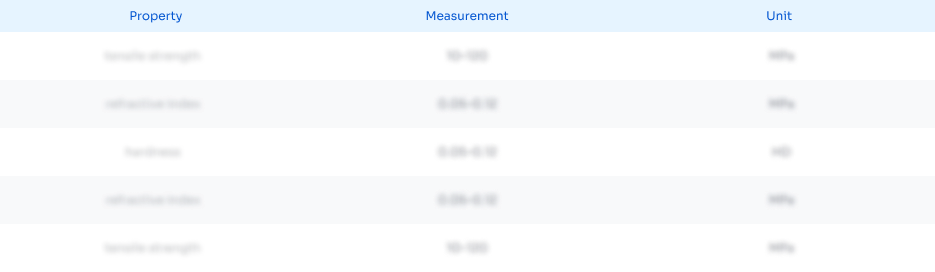
Abstract
Description
Claims
Application Information

- R&D Engineer
- R&D Manager
- IP Professional
- Industry Leading Data Capabilities
- Powerful AI technology
- Patent DNA Extraction
Browse by: Latest US Patents, China's latest patents, Technical Efficacy Thesaurus, Application Domain, Technology Topic, Popular Technical Reports.
© 2024 PatSnap. All rights reserved.Legal|Privacy policy|Modern Slavery Act Transparency Statement|Sitemap|About US| Contact US: help@patsnap.com