Supercharger
A supercharger, bearing bushing technology, applied in the field of exhaust gas turbocharger, can solve the problems of negative impact, blockage wear, high wear, etc.
- Summary
- Abstract
- Description
- Claims
- Application Information
AI Technical Summary
Problems solved by technology
Method used
Image
Examples
Embodiment Construction
[0025] according to Figure 1 to Figure 4 with Figure 8 , the supercharger 1 according to the invention, which can be designed, for example, as an exhaust gas turbocharger 2 for a motor vehicle engine 3 , comprises a bearing arrangement 4 for mounting a shaft 5 . Here, the shaft 5 carries a compressor wheel 6 and a turbine wheel 7 and is mounted via a bearing bush 8 in a bearing housing 9 of the supercharger 1 . Here, the bearing bush 8 is mounted floatingly in a tightly defined manner in the hub of the bearing housing 9 , just as the shaft 5 is mounted floatingly in a tightly defined manner in the bearing sleeve 8 . The stable positioning of the bearing bush 8 in this case is achieved by a pin 10 which engages in the bearing bush 8 radially from the hub. Here, the pin 10 comprises a first part 11 which is rotatably mounted in the bearing housing 9 and engages in a recess 13 (see also in particular Figure 5 with 8 ) in the second part 12, wherein the axis 14 of the first...
PUM
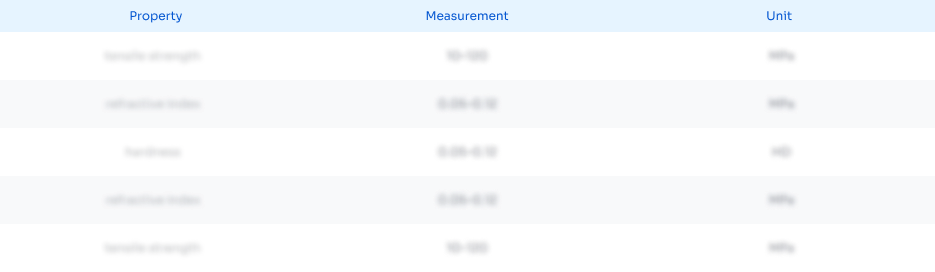
Abstract
Description
Claims
Application Information

- R&D
- Intellectual Property
- Life Sciences
- Materials
- Tech Scout
- Unparalleled Data Quality
- Higher Quality Content
- 60% Fewer Hallucinations
Browse by: Latest US Patents, China's latest patents, Technical Efficacy Thesaurus, Application Domain, Technology Topic, Popular Technical Reports.
© 2025 PatSnap. All rights reserved.Legal|Privacy policy|Modern Slavery Act Transparency Statement|Sitemap|About US| Contact US: help@patsnap.com