Thread winding and threading mechanism and method for cop latches and sewing machine
A bobbin and thread winding technology, which is applied to sewing machine components, bobbin winding in sewing machines, sewing equipment, etc., can solve problems such as low success rate, inability to wind the thread, complex structure, etc., and achieve accurate threading and easy control , the effect of simple structure
- Summary
- Abstract
- Description
- Claims
- Application Information
AI Technical Summary
Problems solved by technology
Method used
Image
Examples
Embodiment 1
[0143] The winding and threading principle of the bobbin winding and threading mechanism 50 in Embodiment 1 is as follows:
[0144] First, the first bobbin core 11 is separated from the first bobbin case 12; as Figure 16 with Figure 17 As shown, after all the remaining sutures 70 on the first bobbin core 11 are removed, the first bobbin core 11 and the first bobbin case 12 are taken off from the fixed shaft 41 by the shuttle gripping mechanism 30, and are placed on the winding shaft backwards. On the bobbin 52 , the first bobbin 11 is locked and fixed on the bobbin 52 under the action of the bobbin fixing spring 57 . Grab the shuttle linear stepping motor reverse action reset, make the hook claw 33 of grabbing the shuttle and loosen the bobbin case plate 17 of the first bobbin case 12, then the hook portion 161 of the clip bar 16 on the first bobbin case 12 does not catch the first bobbin case. The flange 112 of the bobbin core 11; the hook seat moving motor 317 rotates to...
Embodiment 2
[0149] The knife rest installation sleeve 541 is rotatably and movably supported in the main board 21, and the said winding shaft 52 is rotatably installed in the knife rest installation sleeve 541, that is: the knife rest installation sleeve 541 can be rotated and can also be moved forward and backward. move, while the bobbin 52 is only rotatable. Now, the winding drive source 51 is a winding motor fixed on the main board 21, the output end of the winding motor is fixed to the winding shaft 52; Frame installation sleeve 541 moves the knife rest driving source along the axis of the winding shaft 52. The knife rest moving driving source can be an electromagnet, a cylinder, etc., and the output end of the knife rest moving driving source is fixed with a moving plate. The mounting sleeve 541 is rotatably supported in the moving plate. The clamping drive source 53 is a clamping motor fixed on the moving plate. The output end of the clamping motor is fixed to the knife rest mountin...
PUM
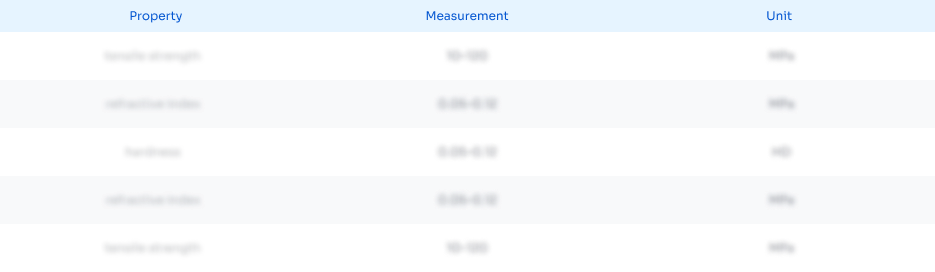
Abstract
Description
Claims
Application Information

- R&D Engineer
- R&D Manager
- IP Professional
- Industry Leading Data Capabilities
- Powerful AI technology
- Patent DNA Extraction
Browse by: Latest US Patents, China's latest patents, Technical Efficacy Thesaurus, Application Domain, Technology Topic, Popular Technical Reports.
© 2024 PatSnap. All rights reserved.Legal|Privacy policy|Modern Slavery Act Transparency Statement|Sitemap|About US| Contact US: help@patsnap.com