Separation method for calcite and magnesite
A separation method, magnesite technology, applied in the field of separation, can solve the problems of large aeration volume, increase the difficulty of target minerals, poor selectivity of target minerals, etc., and achieve the effect of reducing the amount of use
- Summary
- Abstract
- Description
- Claims
- Application Information
AI Technical Summary
Problems solved by technology
Method used
Examples
Embodiment 1
[0023] The flotation of magnesite rough concentrate containing calcite (with a particle size of 0.1-1.5 mm) undergoes the following steps:
[0024] Adjust the slurry concentration of magnesite coarse concentrate to 40wt%; add dispersant water glass 300g / t, and stir for 2 minutes; then add sulfuric acid solution with a concentration of 15wt%, adjust the pH value to 1, and separate the solid and liquid after stirring for 30s; Add the separated solid to 3wt% polyvinyl alcohol aqueous solution to make the slurry concentration 30wt%, stir (1000 r / min) for 2 minutes, add sulfuric acid solution, adjust the pH value to 1, and then undergo conventional flotation to obtain Magnesite concentrate.
[0025] The grade of the obtained magnesite concentrate reached 47.5%, and the recovery rate was close to 91%. Compared with the conventional flotation results, the grade increased by about 1%, and the recovery rate increased by nearly 20%.
Embodiment 2
[0027] The flotation of magnesite coarse concentrate containing calcite (with a particle size of 1-2 mm) undergoes the following steps:
[0028] Adjust the pulp concentration of magnesite coarse concentrate to 30wt%; add dispersant water glass 300g / t, and stir for 2 minutes; then add sulfuric acid solution with a concentration of 25wt%, adjust the pH value to 2, and separate the solid and liquid after stirring for 50s; Add the separated solid to 4wt% polyvinyl alcohol aqueous solution to make the slurry concentration 20wt%, stir (1200 r / min) for 2 minutes, add sulfuric acid solution, adjust the pH value to 2, and then undergo conventional flotation to obtain Magnesite concentrate.
[0029] The grade of the obtained magnesite concentrate reached 47.6%, and the recovery rate was close to 95%. Compared with the conventional flotation results, the grade increased by about 1%, and the recovery rate increased by nearly 25%.
Embodiment 3
[0031] The flotation of magnesite rough concentrate containing calcite (with a particle size of 2 to 3 mm) undergoes the following steps:
[0032] Adjust the pulp concentration of magnesite coarse concentrate to 50wt%; add dispersant water glass 300g / t, and stir for 2 minutes; then add sulfuric acid solution with a concentration of 25wt%, adjust the pH value to 3, and separate the solid and liquid after stirring for 60s; Add the separated solids to 5wt% polyvinyl alcohol aqueous solution to make the slurry concentration 30wt%, stir (1400 r / min) for 2 minutes, add sulfuric acid solution, adjust the pH value to 4, and then undergo conventional flotation to obtain Magnesite concentrate.
[0033] The grade of the obtained magnesite concentrate reached 47.7%, and the recovery rate was close to 96%. Compared with the conventional flotation results, the grade increased by about 1%, and the recovery rate increased by nearly 25%.
PUM
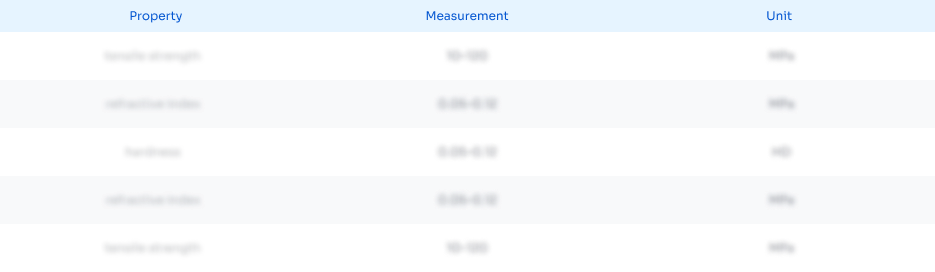
Abstract
Description
Claims
Application Information

- Generate Ideas
- Intellectual Property
- Life Sciences
- Materials
- Tech Scout
- Unparalleled Data Quality
- Higher Quality Content
- 60% Fewer Hallucinations
Browse by: Latest US Patents, China's latest patents, Technical Efficacy Thesaurus, Application Domain, Technology Topic, Popular Technical Reports.
© 2025 PatSnap. All rights reserved.Legal|Privacy policy|Modern Slavery Act Transparency Statement|Sitemap|About US| Contact US: help@patsnap.com