Piezoelectric ultrasonic wave guide probe for steel rail bottom flaw detection and flaw detection method thereof
A piezoelectric ultrasonic and ultrasonic guided wave technology, which is used in material analysis using sonic/ultrasonic/infrasonic waves, processing response signals of detection, measurement devices, etc. Problems such as low modal recognition and inapplicability to production practice, to achieve the effects of high flaw detection efficiency, easy promotion and low cost
- Summary
- Abstract
- Description
- Claims
- Application Information
AI Technical Summary
Problems solved by technology
Method used
Image
Examples
Embodiment 1
[0059] This embodiment provides a piezoelectric ultrasonic guided wave probe, which can be used for rail bottom flaw detection, and makes up for the defect that traditional ultrasonic rail flaw detection technology has a large-area flaw detection blind area in the two sides of the rail bottom. , and the single detection distance is long, the typical single detection distance can reach ten meters to tens of meters, and the flaw detection efficiency is high.
[0060] Such as Figure 1 ~ Figure 4 As shown, the piezoelectric ultrasonic guided wave probe of this embodiment includes an outer shell 1, five piezoelectric units and an interface 2, and each piezoelectric unit includes a piezoelectric wafer 3, a cable 4, a damping block 5, a suction Acoustic filler 6 , elastic element 7 and inner shell 8 .
[0061] Such as Figure 5 ~ Figure 8 As shown, the piezoelectric wafer 3 is selected as a piezoelectric ceramic sheet with a longitudinal vibration mode (LE mode), specifically a pi...
Embodiment 2
[0085] The main features of this embodiment are: the structure of the piezoelectric ultrasonic guided wave probe is the same as that of Embodiment 1, such as Figure 13 As shown, one side of the bottom of the rail is detected, but there are two piezoelectric ultrasonic guided wave probes 9, and the two piezoelectric ultrasonic guided wave probes 9 are placed on the upper surface of the side of the rail bottom of the rail 10, so that the piezoelectric The vibration direction of the wafer 3 is parallel to the length direction of the steel rail 10. During detection, a certain pressure is applied above the piezoelectric ultrasonic guided wave probe 9, so that the piezoelectric wafer 3 at the bottom of the piezoelectric ultrasonic guided wave probe 9 can be closely attached to the steel rail 10. The upper surface of this side of the bottom; the interfaces 2 of the two piezoelectric ultrasonic guided wave probes 9 are respectively connected to the excitation channel and the receiving c...
Embodiment 3
[0087] The main features of this embodiment are: the structure of the piezoelectric ultrasonic guided wave probe is the same as that of Embodiment 1, such as Figure 14 As shown, two piezoelectric ultrasonic guided wave probes 9 are placed on the upper surface of one side of the rail bottom of the rail 10 to detect one side of the rail bottom, but the external equipment includes an external excitation device 12 and an external receiving device 13, namely The excitation and reception functions of the signal are realized by different external devices. The interfaces 2 of the two piezoelectric ultrasonic guided wave probes 9 are respectively connected to the external excitation device 12 and the external receiving device 13, and the piezoelectric ultrasonic wave connected to the external excitation device 12 Guided wave probe 9, the piezoelectric chip 3 realizes the excitation of the guided wave through the inverse piezoelectric effect during detection, and the piezoelectric ultra...
PUM
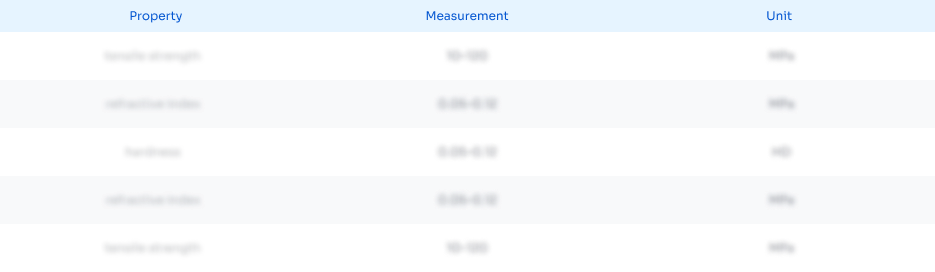
Abstract
Description
Claims
Application Information

- R&D
- Intellectual Property
- Life Sciences
- Materials
- Tech Scout
- Unparalleled Data Quality
- Higher Quality Content
- 60% Fewer Hallucinations
Browse by: Latest US Patents, China's latest patents, Technical Efficacy Thesaurus, Application Domain, Technology Topic, Popular Technical Reports.
© 2025 PatSnap. All rights reserved.Legal|Privacy policy|Modern Slavery Act Transparency Statement|Sitemap|About US| Contact US: help@patsnap.com