Multi-support bidirectional piezoelectric driver
A piezoelectric driver, multi-support technology, applied in the direction of generator/motor, piezoelectric effect/electrostrictive or magnetostrictive motor, electrical components, etc., can solve the rigid contact of the working surface, high working environment requirements, pressure The structure of the electric drive is complicated, etc.
- Summary
- Abstract
- Description
- Claims
- Application Information
AI Technical Summary
Problems solved by technology
Method used
Image
Examples
Embodiment Construction
[0010] refer to figure 1 , figure 2 with image 3 , a multi-support bidirectional piezoelectric driver of the present invention consists of a first piezoelectric vibrator 1, a second piezoelectric vibrator 2, a third piezoelectric vibrator 3, a first support leg 4, a second support leg 5, and a third support leg 6 , the fourth support leg 7, the first foot support 8, the second foot support 9, the third foot support 10 and the fourth foot support 11; wherein:
[0011] The first piezoelectric vibrator 1, the second piezoelectric vibrator 2, and the third piezoelectric vibrator 3 are all made of piezoelectric sheet materials pasted on a rectangular elastic substrate. The first piezoelectric vibrator 1, the second piezoelectric vibrator 2 is sequentially connected with the third piezoelectric vibrator 3, the first support leg 4, the second support leg 5, the third support leg 6 and the fourth support leg 7 are the same rectangular sheet member with certain elasticity, the One...
PUM
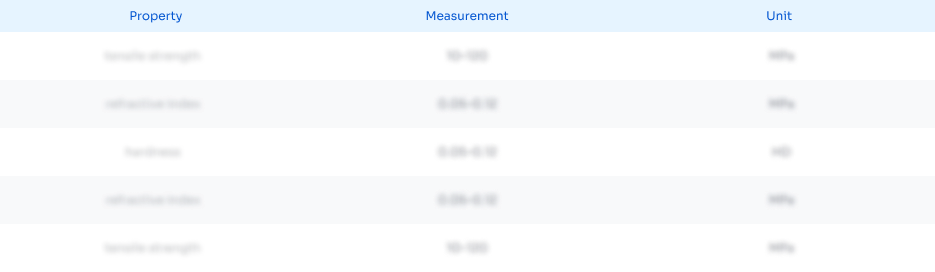
Abstract
Description
Claims
Application Information

- R&D Engineer
- R&D Manager
- IP Professional
- Industry Leading Data Capabilities
- Powerful AI technology
- Patent DNA Extraction
Browse by: Latest US Patents, China's latest patents, Technical Efficacy Thesaurus, Application Domain, Technology Topic, Popular Technical Reports.
© 2024 PatSnap. All rights reserved.Legal|Privacy policy|Modern Slavery Act Transparency Statement|Sitemap|About US| Contact US: help@patsnap.com