Bearing test device for applying radial alternating load based on synchronous belt drive mechanism
A synchronous belt drive, alternating load technology, applied in the direction of mechanical bearing testing, can solve problems such as single loading characteristics, inability to achieve variable load loading, difficult to carry out engine dynamic load bearing tests, etc., to achieve good results and flexible adjustment. Effect
- Summary
- Abstract
- Description
- Claims
- Application Information
AI Technical Summary
Problems solved by technology
Method used
Image
Examples
Embodiment 1
[0031] A bearing test device for applying radial alternating loads based on a synchronous belt transmission mechanism, such as figure 1 As shown, the device includes a computer 1, a drive motor 2, a coupling 3, a torque meter 4, a fixed fixture A5, an oil supply system 6, a radial alternating load loading module 7, a movable fixture 8, a fixed fixture B 9, a rotating Shaft 10, test bearing B11, test bearing B 12, test bearing A13, test bearing A14, working platform 15. Among them, such as figure 2 As shown, the radial alternating load loading module 7 includes a temperature sensor 16, a rotating motor A17, a synchronous belt transmission mechanism A18, a spring A19, a connecting device A20, a rotating motor B 21, a synchronous belt transmission mechanism B22, a spring B 23, and a connecting device B 24, connecting device C 25, spring C 26, synchronous belt drive mechanism C 27, rotating motor C28, connecting device D 29, spring D 30, synchronous belt driving mechanism D 31, ...
Embodiment 2
[0037] A bearing test device based on a synchronous belt drive mechanism that applies radial alternating loads, its structure is roughly the same as that of Embodiment 1, the difference is that the diameter of the driving wheel in this embodiment is the same as that of the driven wheel.
PUM
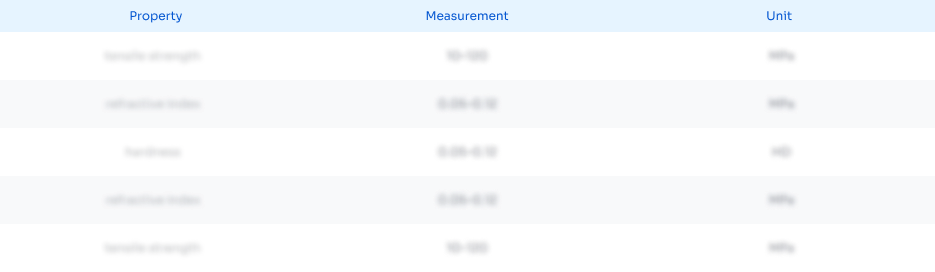
Abstract
Description
Claims
Application Information

- R&D
- Intellectual Property
- Life Sciences
- Materials
- Tech Scout
- Unparalleled Data Quality
- Higher Quality Content
- 60% Fewer Hallucinations
Browse by: Latest US Patents, China's latest patents, Technical Efficacy Thesaurus, Application Domain, Technology Topic, Popular Technical Reports.
© 2025 PatSnap. All rights reserved.Legal|Privacy policy|Modern Slavery Act Transparency Statement|Sitemap|About US| Contact US: help@patsnap.com