Forging mold
A technology of die and die base, which is applied in the direction of manufacturing tools, forging/pressing/hammer devices, forging/pressing/hammering machines, etc., can solve the problems of waste of resources and complicated structure of ejector devices, and achieve energy saving and simple structure. Effect
- Summary
- Abstract
- Description
- Claims
- Application Information
AI Technical Summary
Problems solved by technology
Method used
Image
Examples
Embodiment Construction
[0012] The present invention will be further described below in conjunction with the accompanying drawings and embodiments.
[0013] figure 1 Among them, a forging die includes an upper mold base and a lower mold base that cooperate with each other. The upper mold base includes a punch mounting base 1, and the punch mounting base 1 is connected with a punch 3 through a connecting rod 2. The lower mold base is provided with There is a forging groove 6 matched with the punch 3, and an ejector device is provided on the lower mold base, and the ejector device includes a ejector rod 7 that runs through the forging groove 6, and the ejector rod 7 is connected with a driven rod 5, and the punch mounting seat 1 is connected with the active rod 4 that is compatible with the driven rod 5, and the lower end of the driven rod 5 is also connected with a return spring 9.
[0014] There are three push rods 7 and they are triangularly distributed. One end of any push rod 7 extends out of the...
PUM
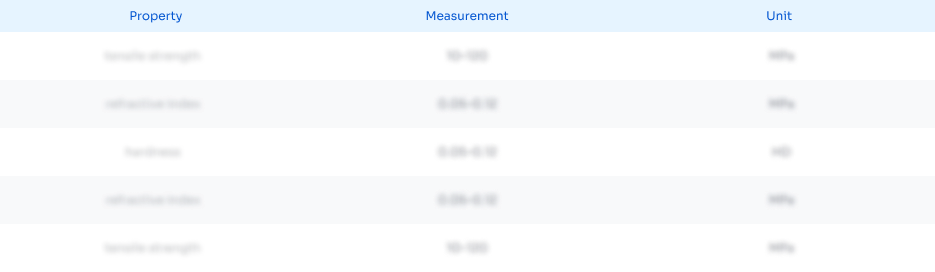
Abstract
Description
Claims
Application Information

- R&D
- Intellectual Property
- Life Sciences
- Materials
- Tech Scout
- Unparalleled Data Quality
- Higher Quality Content
- 60% Fewer Hallucinations
Browse by: Latest US Patents, China's latest patents, Technical Efficacy Thesaurus, Application Domain, Technology Topic, Popular Technical Reports.
© 2025 PatSnap. All rights reserved.Legal|Privacy policy|Modern Slavery Act Transparency Statement|Sitemap|About US| Contact US: help@patsnap.com