Simulating calculation method for pre-clamping stress of end non-identical structure type oblique type change section flat springs
A simulation calculation, non-isomorphic technology, applied in the direction of calculation, design optimization/simulation, special data processing applications, etc., can solve the problem of complex calculation of clamping stiffness, non-isomorphic inclined-line variable-section leaf spring at the end that has not been given and other issues, to achieve the effect of reducing design development and test costs, improving design level, and speeding up development
- Summary
- Abstract
- Description
- Claims
- Application Information
AI Technical Summary
Problems solved by technology
Method used
Image
Examples
Embodiment 1
[0031] Example 1: half of the working length L of a non-equal-structured oblique-line type variable-section leaf spring at a certain end T =550mm, half the length L of the straight section of the root clamped by the saddle bolt 0 =50mm, width b=60mm, elastic modulus E=200GPa. The number of leaf springs n=3, the thickness h of the straight section at the root of each leaf spring 2 =12mm, the thickness of the straight section at the end of each leaf spring is h 11 = 8mm, h 12 = 7mm, h 13 = 6mm. The thickness ratios of the oblique segments of each leaf spring are β 1 = h 11 / h 2 =0.6667,β 2 = h 12 / h 2 = 0.5833, β 3 = h 13 / h 2 = 0.50. The design value of the free tangent arc height of each leaf spring is H g10 =95.2mm,H g20 =101mm, H g30 = 107.7mm. Root gasket thickness δ c =3mm, end gasket thickness δ e = 6mm. According to the number of leaf springs, elastic modulus, the thickness of the root gasket and the end gasket, the structural parameters of each leaf...
Embodiment 2
[0062] Embodiment 2: the width b=60mm of a non-equal few-piece slanted-line variable-section leaf spring at a certain end, and half the effective length L T =550mm, half the length L of the straight section of the root clamped by the saddle bolt 0 =50mm, elastic modulus E=200GPa. The number of leaf springs n=4, the thickness h of the straight section at the root of each leaf spring 2 = 14mm, the thickness h of the straight section at the end 11 = 9mm, h 12 = 8mm, h 13 = 7mm, h 14 = 6 mm. The thickness ratios of the oblique segments of each leaf spring are β 1 = h 11 / h 2 = 0.6429, β 2 = h 12 / h 2 = 0.5714, β3 = h 13 / h 2 =0.50,β 4 = h 14 / h 2 = 0.4286. The design value of the free tangent arc height of each leaf spring is H g10 =90.4mm, H g20 =95.4mm,H g30 =99.7mm,H g40 = 104.7mm. Root gasket thickness δ c =3mm, end gasket thickness δ e = 6mm. According to the number of leaf springs, elastic modulus, the thickness of the root gasket and the end gasket,...
PUM
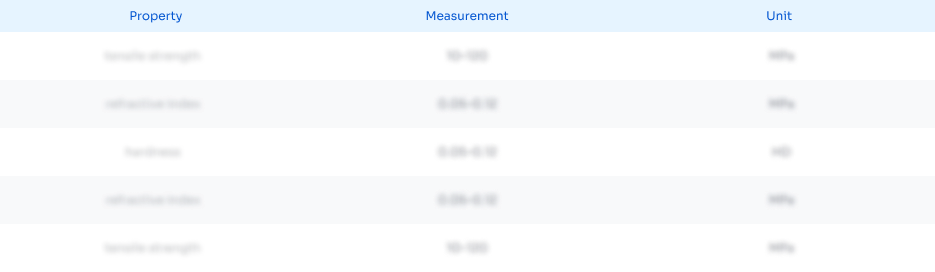
Abstract
Description
Claims
Application Information

- Generate Ideas
- Intellectual Property
- Life Sciences
- Materials
- Tech Scout
- Unparalleled Data Quality
- Higher Quality Content
- 60% Fewer Hallucinations
Browse by: Latest US Patents, China's latest patents, Technical Efficacy Thesaurus, Application Domain, Technology Topic, Popular Technical Reports.
© 2025 PatSnap. All rights reserved.Legal|Privacy policy|Modern Slavery Act Transparency Statement|Sitemap|About US| Contact US: help@patsnap.com