Printing ink concentration increasing technology for plastic printing
A technology of plastic printing and ink, applied in the field of ink thickening, can solve the problems of difficult drying of ink and poor affinity, and achieve the effects of improving thixotropic properties, enhancing PH stability and good dispersibility
- Summary
- Abstract
- Description
- Claims
- Application Information
AI Technical Summary
Problems solved by technology
Method used
Examples
Embodiment 1
[0020] A plastic printing ink concentration thickening process, the specific steps of the plastic printing ink concentration thickening process are as follows:
[0021] S1: Material selection: mixed solvent of terpineol and diethylene glycol as ink solvent, polyketone high hydroxyl resin as ink resin, pigment, additive and thickener;
[0022] S2: Raw material ratio: Take 30 parts of terpineol: diethylene glycol = 3:1 mixed solvent, 24 parts of polyketone high-hydroxyl resin, 22 parts of pigment, 4 parts of auxiliary agent, 4 parts of thickener for spare ;
[0023] S3: Preparation of thickener: 1.2 parts by mass of aluminum isopropoxide and 0.8 parts by mass of 2-ethylhexanoic acid-1-methylethyl ester were mixed and stirred at 130°C for 1.5h, then 3 parts by mass of deionized water was added and heated at 160°C Pre-emulsify for 0.5h after stirring evenly under high pressure, add 0.2 parts by mass of initiator in the flask, react until no reflux occurs, stop the reaction and fi...
Embodiment 2
[0033] A plastic printing ink concentration thickening process, the specific steps of the plastic printing ink concentration thickening process are as follows:
[0034] S1: Material selection: mixed solvent of terpineol and diethylene glycol as ink solvent, polyketone high hydroxyl resin as ink resin, pigment, additive and thickener;
[0035] S2: Raw material ratio: Take 30 parts of terpineol: diethylene glycol = 3:1 mixed solvent, 24 parts of polyketone high-hydroxyl resin, 22 parts of pigment, 4 parts of auxiliary agent, 4 parts of thickener for spare ;
[0036] S3: Preparation of thickener: 1.3 parts by mass of aluminum isopropoxide and 0.9 parts by mass of 2-ethylhexanoic acid-1-methylethyl ester were mixed and stirred at 130°C for 1.5h, 4 parts by mass of deionized water was added, and heated at 160°C Pre-emulsify for 0.5h after stirring evenly under high pressure, add 0.3 parts by mass of initiator in the flask, react until no reflux occurs, stop the reaction and filter...
Embodiment 3
[0046] A plastic printing ink concentration thickening process, the specific steps of the plastic printing ink concentration thickening process are as follows:
[0047] S1: Material selection: mixed solvent of terpineol and diethylene glycol as ink solvent, polyketone high hydroxyl resin as ink resin, pigment, additive and thickener;
[0048] S2: Raw material ratio: Take 30 parts of terpineol: diethylene glycol = 3:1 mixed solvent, 24 parts of polyketone high-hydroxyl resin, 22 parts of pigment, 4 parts of auxiliary agent, 4 parts of thickener for spare ;
[0049]S3: Preparation of thickener: Mix 1.4 parts by mass of aluminum isopropoxide and 1.0 parts by mass of 2-ethylhexanoic acid-1-methylethyl ester at 130°C for 1.5h, add 5 parts by mass of deionized water, and heat at 160°C After stirring evenly, pre-emulsify for 0.5h, add 0.4 parts by mass of initiator in the flask, react until no reflux occurs, stop the reaction and filter to obtain a white emulsion;
[0050] S4: Colo...
PUM
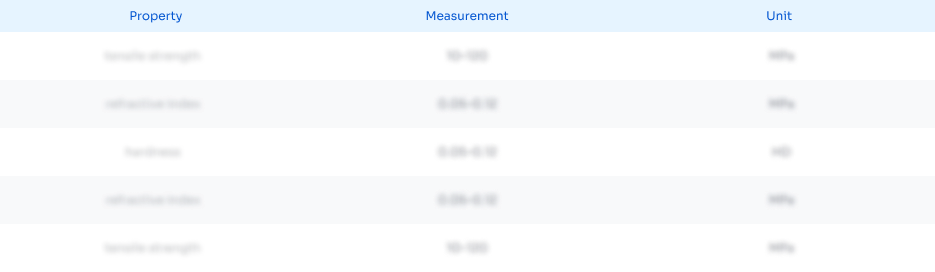
Abstract
Description
Claims
Application Information

- R&D Engineer
- R&D Manager
- IP Professional
- Industry Leading Data Capabilities
- Powerful AI technology
- Patent DNA Extraction
Browse by: Latest US Patents, China's latest patents, Technical Efficacy Thesaurus, Application Domain, Technology Topic, Popular Technical Reports.
© 2024 PatSnap. All rights reserved.Legal|Privacy policy|Modern Slavery Act Transparency Statement|Sitemap|About US| Contact US: help@patsnap.com