Turbine runner three-dimensional curved surface blade electroslag smelting casting direct forming method
A technology of electroslag casting and three-dimensional curved surface, which is applied in the field of electroslag casting to produce turbine runner blade castings. It can solve the problems of inability to cast complex special-shaped parts, achieve high resistance to crack formation and expansion, reduce pollution, and have high dimensional accuracy. Effect
- Summary
- Abstract
- Description
- Claims
- Application Information
AI Technical Summary
Problems solved by technology
Method used
Image
Examples
Embodiment 1
[0055] Such as Figure 1-Figure 2 As shown, in this embodiment, the fixed electrode 2 and the crystallizer are assembled according to the process requirements for the electroslag casting of the blank of the runner blade of the Francis hydro-generator, and the consumable electrode includes two movable electrodes 1 . The fixed electrode 2, a movable electrode 1 and the power source I7 form a power circuit A, and the other movable electrode 1, the bottom pad 6 and the power source II8 form a power circuit B. During the casting process, the power circuit B heats the slag layer 3 to obtain a liquid molten slag layer, which creates conditions for the work of the power circuit A. The power circuit A enhances the fluidity of the metal in this area and completes the casting of the complex cavity area. During the process, the self-consumable electrode is continuously consumed, and the active electrode 1 is continuously replenished until the casting is melted and casted into a solidified...
Embodiment 2
[0057] Such as Figure 1-Figure 2 As shown, in this embodiment, the electroslag casting of the blank of the runner blade of the axial flow (tubular) hydroelectric generator uses the movable electrode 1 and the fixed electrode 2 in the mold cavity 5 . Before the crystallizer assembly box, the fixed electrode 2 is fixed at the designated position of the mold cavity 5. After the movable electrode 1 is installed in place, a safe distance is kept between them, and the movable electrode 1 continuously performs self-consumption during the casting process. In addition, in a special area, the fixed electrode 2 contacts the liquid molten slag layer 3 and starts to conduct the power circuit, and the electrode starts to melt.
[0058] The results of the examples show that the present invention is a nearly net-shape integral casting blank manufacturing technology, especially an electroslag casting method for one-time forming of the runner blade of a hydroelectric generator, and the produce...
PUM
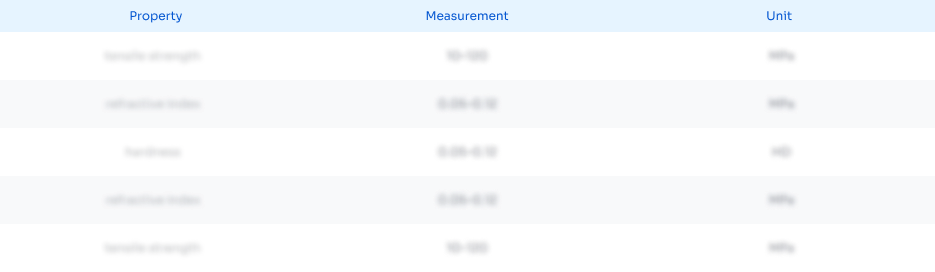
Abstract
Description
Claims
Application Information

- R&D Engineer
- R&D Manager
- IP Professional
- Industry Leading Data Capabilities
- Powerful AI technology
- Patent DNA Extraction
Browse by: Latest US Patents, China's latest patents, Technical Efficacy Thesaurus, Application Domain, Technology Topic, Popular Technical Reports.
© 2024 PatSnap. All rights reserved.Legal|Privacy policy|Modern Slavery Act Transparency Statement|Sitemap|About US| Contact US: help@patsnap.com