Reliability modeling method based on cumulative fatigue damage
A technology of cumulative damage and modeling method, which is applied in special data processing applications, instruments, electrical digital data processing, etc. It can solve the problems of large amount of calculation, difficulty in parameter distribution of random factors, and long time-consuming, etc., and achieve high calculation accuracy. Effect
- Summary
- Abstract
- Description
- Claims
- Application Information
AI Technical Summary
Problems solved by technology
Method used
Image
Examples
specific Embodiment approach 1
[0022] Specific embodiment one: a kind of reliability modeling method based on fatigue cumulative damage comprises the following steps:
[0023]Fatigue failure is the most important way for aircraft structures to fail due to multi-structural design and random dynamic loads during flight. The evaluation methods of aircraft structural reliability have been developed for more than 30 years, and are generally divided into deterministic analysis methods and probabilistic analysis methods. Among the deterministic analysis methods, the fatigue stress life method is more representative, and the probabilistic damage tolerance method is more studied in the probabilistic analysis methods. The simplicity and practicality of the fatigue stress-life method make it widely used to determine the fatigue life of aircraft structures (D.T.Rusk and P.Hoffman, 5Th Joint NASA / FAA / DoDConference on Aging Aircraft, 2001.), but due to the Existence often causes the structure to be repaired or decommiss...
specific Embodiment approach 2
[0029] Specific embodiment two: the difference between this embodiment and specific embodiment one is: the expression of the fatigue stress life method in the step one is:
[0030] Miner's linear cumulative damage theory believes that under cyclic loading, the relationship between fatigue damage and the number of load cycles is linear, and fatigue damage can be added linearly, and each stress is independent and uncorrelated with each other. When the accumulated damage reaches 1 , the specimen undergoes fatigue failure.
[0031]
[0032] dam i =n i / N i (3)
[0033] where dam i is the damage component, D is the total cumulative damage, n i For the specimen at the stress level S i The number of working cycles under the action of N i For the specimen at stress level S i The number of destruction cycles below.
[0034] Based on Miner's linear cumulative damage theorem, the fatigue stress-life method directly correlates the load and life of the structure. The fatigue ...
specific Embodiment approach 3
[0036] Embodiment 3: The difference between this embodiment and Embodiment 1 or 2 is that the crack interference life model of the probabilistic damage tolerance in the first step is:
[0037] The damage tolerance is established on the basis of deterministic fracture mechanics (Deterministic Fracture Mechanics, DFM), its analysis process and results have the meaning of the median value, and its reliability is calculated by dividing the deterministic crack growth life by the specified dispersion factor ensure. The probabilistic damage tolerance analysis method fully considers the dispersion of various factors affecting the crack growth life on the basis of damage tolerance, and studies its probability characteristics, so as to accurately and quantitatively calculate the reliability corresponding to a given crack growth life.
[0038]
[0039] where f a (a,t) is the crack distribution density function when the flight time is t, f ac (a c ) is the size distribution density ...
PUM
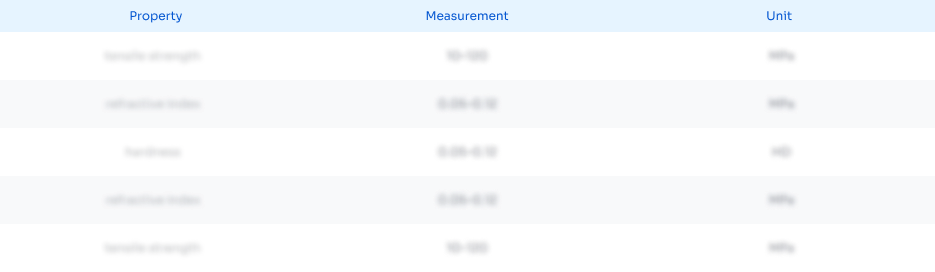
Abstract
Description
Claims
Application Information

- R&D
- Intellectual Property
- Life Sciences
- Materials
- Tech Scout
- Unparalleled Data Quality
- Higher Quality Content
- 60% Fewer Hallucinations
Browse by: Latest US Patents, China's latest patents, Technical Efficacy Thesaurus, Application Domain, Technology Topic, Popular Technical Reports.
© 2025 PatSnap. All rights reserved.Legal|Privacy policy|Modern Slavery Act Transparency Statement|Sitemap|About US| Contact US: help@patsnap.com