Compact type compliant orthogonal displacement amplifying mechanism with gain being increased with input force
A technology of displacement amplifying mechanism and input force, applied in the directions of manipulators, manufacturing tools, etc., can solve the problems of reduced mechanism gain, disadvantage, disadvantage of compactness, etc., and achieve the effect of improving accuracy and increasing input force
- Summary
- Abstract
- Description
- Claims
- Application Information
AI Technical Summary
Problems solved by technology
Method used
Image
Examples
Embodiment
[0039] Such as Figure 1 to Figure 3 As shown, the present invention is a compact compliant orthogonal displacement amplifying mechanism whose gain increases with the input force, which includes a rigid input end 1 for the input force, a left rigid output end 6, a right rigid output end 9, and a left variable section Beam, right variable section beam, left undetermined equal straight beam 7 and right undetermined equal straight beam 8, wherein the left variable section beam, left rigid output end 6 and left undetermined equal straight beam 7 are connected in sequence, and the left variable section beam is far away from the left rigid One end of the output end 6 is connected to the lower end surface of the rigid input end 1, and the right variable-section beam, the right rigid output end 9 and the right undetermined straight beam 8 are connected in sequence, and the end of the right variable-section beam far away from the right rigid output end 9 is connected to the rigid input ...
PUM
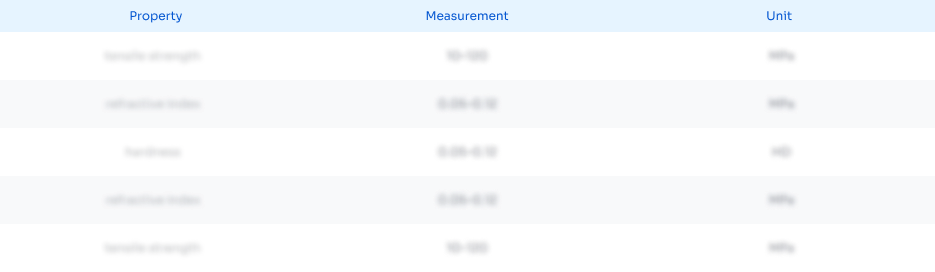
Abstract
Description
Claims
Application Information

- R&D
- Intellectual Property
- Life Sciences
- Materials
- Tech Scout
- Unparalleled Data Quality
- Higher Quality Content
- 60% Fewer Hallucinations
Browse by: Latest US Patents, China's latest patents, Technical Efficacy Thesaurus, Application Domain, Technology Topic, Popular Technical Reports.
© 2025 PatSnap. All rights reserved.Legal|Privacy policy|Modern Slavery Act Transparency Statement|Sitemap|About US| Contact US: help@patsnap.com