Feeding cooling system for printing machine
A cooling system and printing machine technology, applied in the field of mechanical equipment, can solve problems such as layout defects, particles falling on the cardboard, affecting printing quality, etc., and achieve the effect of improving printing quality
- Summary
- Abstract
- Description
- Claims
- Application Information
AI Technical Summary
Problems solved by technology
Method used
Image
Examples
Embodiment Construction
[0035] As shown in the figure, the present invention includes a paper section, a printing machine 10, a cooling section 20 and a discharge section,
[0036] The paper loading section includes a paper loading device and a dust cleaning device,
[0037] The paper loading device includes a frame 1, a double-axis motor 2, a pair of chain boxes 3, a pair of chains 4, a stacking plate 5 and one or a group of pickup wheels 6,
[0038] One section of the frame 1 is provided with a material inlet, and the other end is provided with a material outlet,
[0039] The double-axis motor 2 is fixedly installed on the top of the frame 1,
[0040] A pair of chain boxes 3 are installed on both sides of the bottom of the frame 1 respectively,
[0041] A pair of chains 4 are respectively connected to the power output end of the biaxial motor 2 and the sprocket wheels in the pair of chain boxes 3,
[0042] Both sides of the stacking plate 5 are fixedly connected on a pair of chains 4, and move u...
PUM
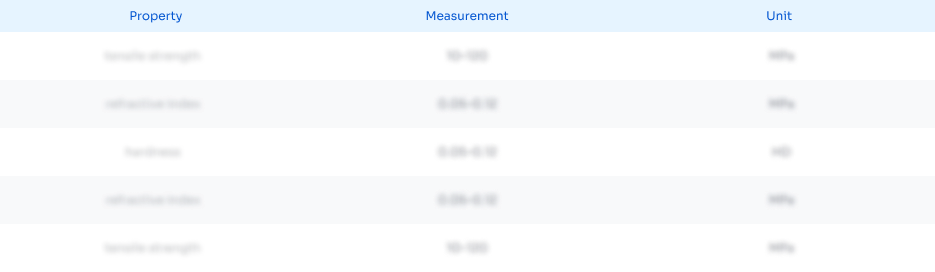
Abstract
Description
Claims
Application Information

- Generate Ideas
- Intellectual Property
- Life Sciences
- Materials
- Tech Scout
- Unparalleled Data Quality
- Higher Quality Content
- 60% Fewer Hallucinations
Browse by: Latest US Patents, China's latest patents, Technical Efficacy Thesaurus, Application Domain, Technology Topic, Popular Technical Reports.
© 2025 PatSnap. All rights reserved.Legal|Privacy policy|Modern Slavery Act Transparency Statement|Sitemap|About US| Contact US: help@patsnap.com